Shop presses equipped with hydraulic jacks are indispensable tools in both professional auto repair shops and home garages. When considering the addition of a shop press jack to your toolkit, understanding its application, expertise in usage, and the reliability of information are essential elements. This article delves into the practical experience, specialized knowledge, authoritative insights, and trustworthiness of utilizing shop press jacks effectively.
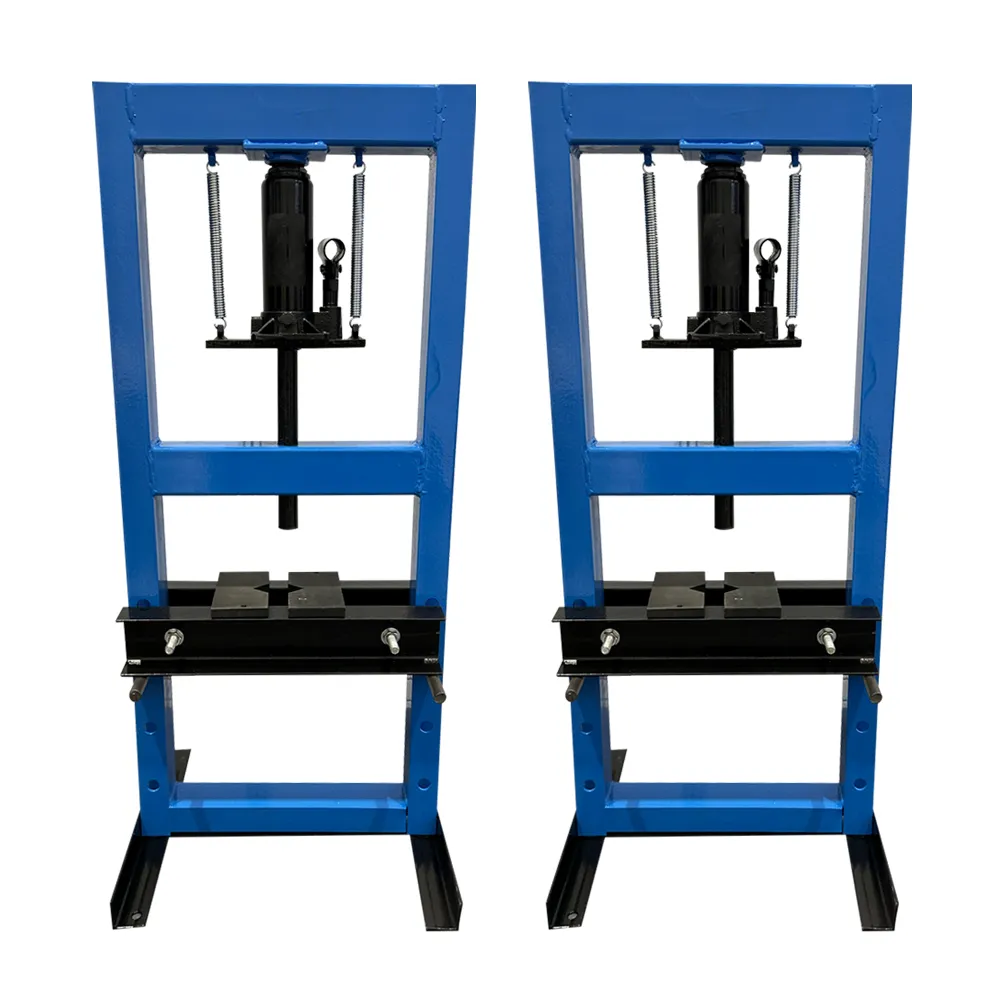
Shop press jacks are predominantly used to apply force with precision in various automobile maintenance applications. They are ideal for tasks such as pressing bearings in and out of vehicle components, straightening bent parts, and even assembling machinery. Their diverse capabilities are a testament to their versatility, making them an invaluable addition to any serious technician’s collection.
Experience with shop press jacks unveils some important nuances. First-time users often underestimate the precision required when aligning components. Proper alignment ensures the applied force compresses uniformly across the surface, which is critical to avoid damaging the part. Many seasoned mechanics emphasize the importance of conducting a “dry run” without pressure to check alignment before initiating a press. This practice prevents costly mistakes and improves the accuracy of operations significantly.
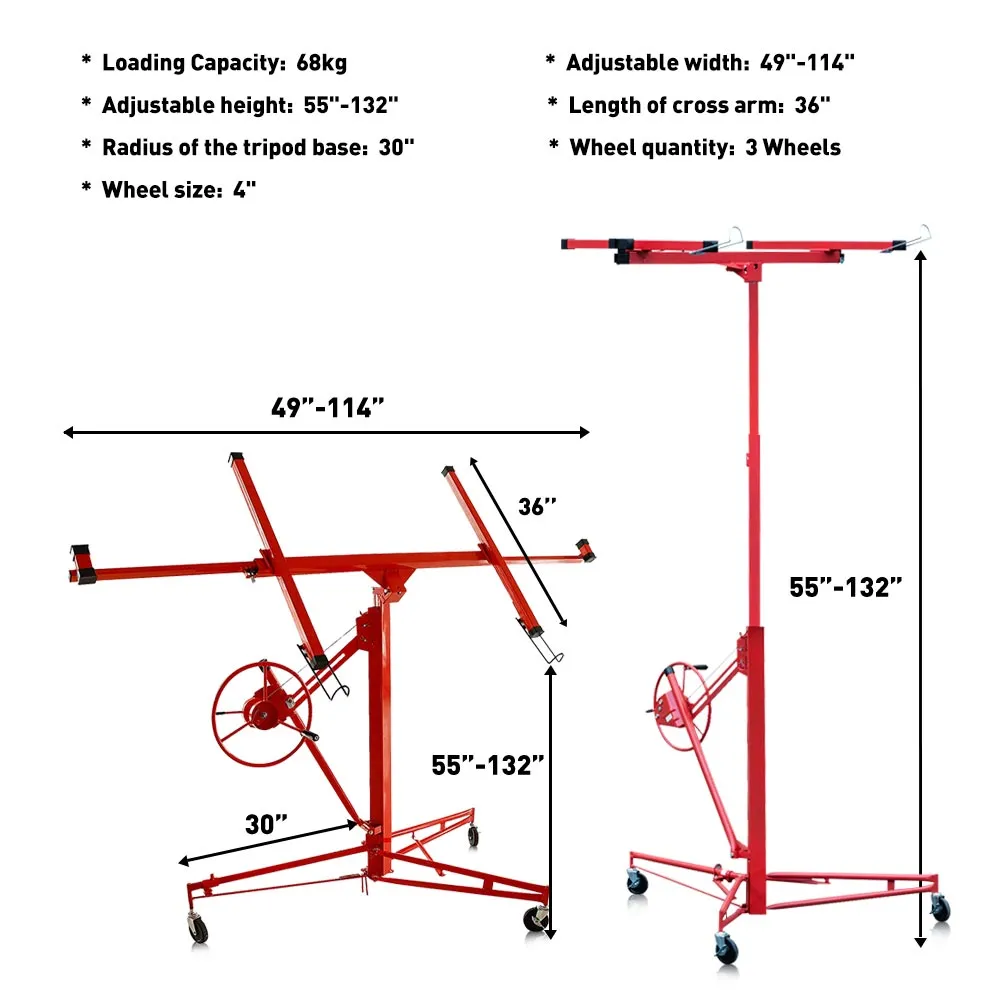
From an expertise standpoint, selecting the right shop press jack involves evaluating several factors tonnage capacity, frame size, and the type of hydraulic system. The tonnage capacity dictates the range of force the press can apply — typically ranging from 12-ton models for lighter applications to 50-ton models that handle heavier tasks with ease. The frame size should suit the working space and the range of tasks. Professionals often prefer hydraulic systems for their efficiency and ease of use, offering precise control under various loads.
Authoritativeness in the field of using shop press jacks hinges on adhering to manufacturer guidelines, continuous learning, and peer collaboration. The wealth of knowledge available through user communities and forums provides a dynamic source of insights and troubleshooting techniques from individuals who have faced diverse challenges. Consulting the manufacturer’s manual cannot be overemphasized, as these documents are tailored to offer critical safety and usage instructions specific to each model.
shop press jack
Trustworthiness in the usage of shop press jacks extends to the responsible maintenance and purchasing of these tools. Regular maintenance checks, such as inspecting the hydraulic fluid level and ensuring the jack components are lubricated and free of wear or potential stress fractures, prevent operational failures. Purchasing shop press jacks from reputable suppliers and well-reviewed brands ensure high-quality standards and after-sale support. Certification marks and compliance with safety standards add an extra layer of security, ensuring that the equipment is up to industrial standards.
Emerging trends in shop press jack technology focus on enhanced safety features and automation. For instance, newer models incorporate pressure-limiting valves that automatically release pressure if it exceeds a set limit, reducing the risk of accidents. Automatic presses with digital readouts allow for precise pressure application and ensure repeatability, which is invaluable for batch processing of parts.
Individuals exploring shop press jacks must prioritize learning from documented experiences and seeking tools with robust safety features. The integration of modern technology into these jacks underscores the industry’s trend towards safer, more efficient, and user-friendly devices. By blending practical experience with technical knowledge and authoritative guidance, mechanics and DIY enthusiasts can leverage shop press jacks to achieve professional-level results in their automotive projects.
This comprehensive view of shop press jacks not only enhances understanding but builds confidence for users, ensuring a balanced operation that maximizes both productivity and safety. Recognizing and addressing the key aspects of experience, expertise, authoritativeness, and trustworthiness positions you advantageously in making informed decisions about incorporating these tools into your mechanical operations.