Bottle jacks, often perceived as innocuous trailblazers of lifting mechanics, have carved a niche in the realm of hydraulic pressing. These versatile tools are not just confined to automotive repairs and maintenance but are gaining momentum as indispensable components in hydraulic presses. The migration from mere vehicle lifts to precision instrumentalists in industrial applications heralds an era of increased efficiency and reliability.
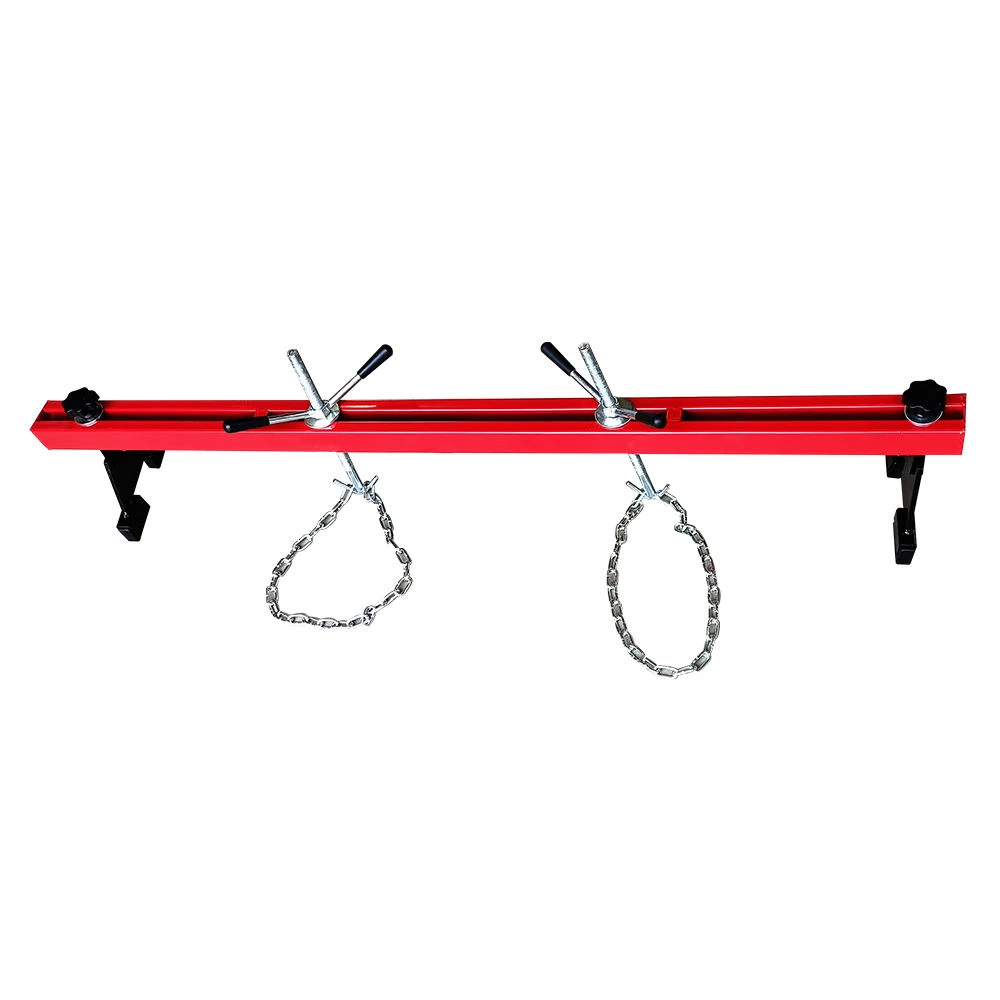
The journey begins with understanding the fundamental mechanics of a bottle jack. Traditionally, a bottle jack operates through a hydraulic ram mechanism, utilizing Pascal's Law to multiply force. The simplicity of design— a vertical cylinder with a piston assembly, enhanced by a sturdy base— provides formidable lifting power. This basic architecture is a cornerstone of its adaptability in pressing applications.
In the world of hydraulic presses, the bottle jack transforms from a lifting device to a precision-controlled force applicator. Its compact size merges with an incredible lifting capacity, offering a perfect synergy between space efficiency and power. For small to medium hydraulic press operations, the bottle jack is the epitome of operational excellence; it replaces bulky mechanical actuators with a sleeker, more efficient hydraulic force generation system.
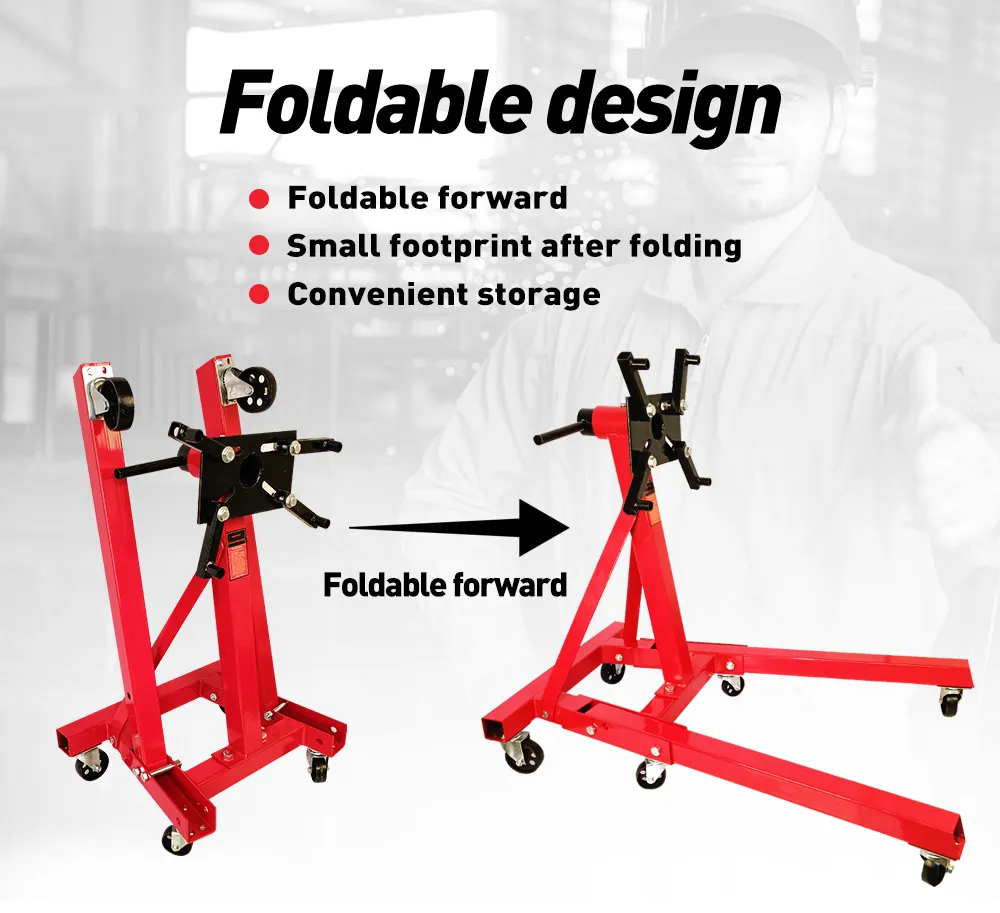
The adaptability of bottle jacks in presses is largely due to their hydraulic nature. In a press setup, they deliver consistent pressure over a defined surface area, allowing for precise metal forming, bearing pressing, or even intricate woodworking tasks. This consistent pressure application is crucial, especially when uniformity and precision are paramount in manufacturing processes.
The expertise in utilizing bottle jacks within presses lies in selecting the appropriate jack specification for the intended application. Important considerations include the weight to be pressed, the stroke length required, and the operational pressure constraints. Seasoned professionals recommend opting for jacks with a little extra capacity than needed, offering a buffer zone and ensuring longevity and safety in its operation.
bottle jack for press
Furthermore, the transition of bottle jacks into press tools is fortified by their ease of maintenance. Hydraulic systems require regular fluid checks and seal inspections to maintain optimum efficiency. Experienced users emphasize maintaining a contamination-free hydraulic fluid environment, as impurities can lead to seal damage or cylinder scoring, directly affecting press performance.
A notable edge that bottle jacks provide in a press setup is the inherent flexibility. Unlike dedicated hydraulic press systems, which may require extensive setups and calibrations, bottle jacks offer an easy plug-and-play solution. This simplicity not only minimizes downtime but is a boon for small workshops and enthusiasts who seek to integrate hydraulic pressing capabilities without substantial investments.
The authority of bottle jacks in presses is further endorsed by their reliability. Anecdotes from industry veterans highlight their longevity, with many attributing years of dependable service to routine maintenance and adherence to operation guidelines. This trust, cultivated through real-world applications and consistent performance, establishes bottle jacks as vital components in both amateur and professional setups.
Emerging from the workshops and garages, bottle jacks are sculpting a new landscape in the pressing industry. Their rise is marked by an endorsement from experts who recognize the balance they strike between power, flexibility, and cost-efficiency. As industries evolve and the demand for versatile, reliable tools increases, the bottle jack stands as a testament to innovation in hydraulic technology.
In conclusion, the transformation of the bottle jack from a lift device to a high-precision force applicator in presses is a narrative of innovation meeting necessity. Through experience, expertise, and a track record of reliability, bottle jacks have successfully pitched themselves as credible and authoritative tools that reshape notions of hydraulic efficacy in pressing operations.