Designing an H-frame hydraulic press involves a complex yet rewarding process, one that requires a blend of engineering acumen, creativity, and precision. This machinery is essential across industries, be it automotive, aerospace, or manufacturing, due to its ability to exert immense force within a compact structure. The design process, therefore, is pivotal not just for functionality, but for safety, efficiency, and longevity.
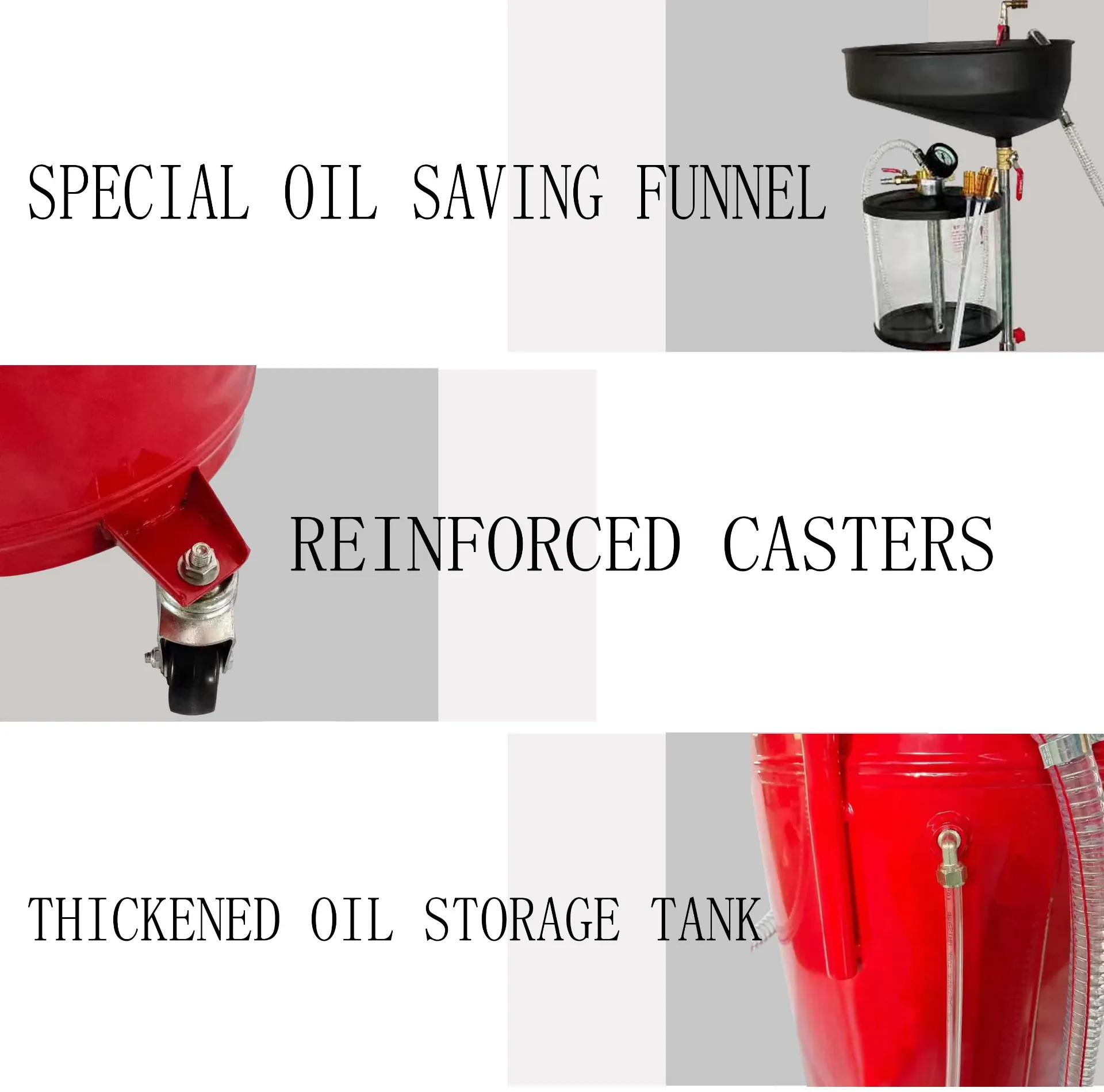
Understanding the core components and their interactions is the foundation of any successful H-frame hydraulic press design. The frame itself must be robust enough to handle the maximum load without deformation. Utilizing high-quality steel or custom alloys tailored to specific industrial needs enhances both stability and durability. The girder-like configuration aids in distributing stress evenly, thereby minimizing wear and tear and extending the machine’s lifespan.
Hydraulic systems are the heart of these presses. Expertise in fluid dynamics is crucial, as the hydraulic system must precisely control the motion and force exerted. Selection of the right hydraulic cylinders, pumps, and valves ensures the system’s responsiveness and power efficiency. It’s essential to incorporate advanced control systems, possibly computerized or IoT-enabled, for real-time monitoring and adjustments, which significantly enhance operational precision.

Operator safety and user-friendliness cannot be overstressed in H-frame press design. Ensuring that every design aspect complies with international safety standards and regulations is non-negotiable. Implementing safety mechanisms, such as emergency stop buttons, pressure relief valves, and automatic shutdown features, helps in preventing accidents and machinery damage. Ergonomic considerations, like intuitive control panels and adjustable working heights, not only boost productivity but also enhance user well-being.
Accurate and comprehensive technical documentation, preferably in PDF format, is indispensable. This documentation should cover every aspect of the design—from detailed schematics and specifications to maintenance guides and troubleshooting tips. Not only does this facilitate seamless integration and usage, but it also establishes your authority and reliability in the market, building trust with users and stakeholders.
h frame hydraulic press design pdf
Sustainability is another growing consideration in hydraulic press design. Choosing eco-friendly materials, minimizing waste in production, and designing for energy efficiency can significantly reduce the environmental impact. Incorporating features such as energy-saving modes or using biodegradable hydraulic fluids positions your product as forward-thinking and responsible, appeals to environmentally conscious consumers, and complies with increasingly strict environmental legislation.
The longevity and adaptability of the machine in the ever-evolving industrial landscape require foresight in design. Designing with modular components allows for easy upgrades and maintenance, thus ensuring the press remains at the cutting edge of technology without needing complete overhauls. Such foresight not only extends the machine’s usable life but also maximizes customer ROI, which is a significant selling point.
Harnessing customer feedback is vital in refining the design and performance. Engaging with users to understand their challenges and suggestions can provide invaluable insights, enhancing future iterations. Establishing feedback loops or user forums helps keep your product aligned with user needs and market dynamics, strengthening brand loyalty and market presence.
In essence, crafting the ideal H-frame hydraulic press demands more than just technical skills—it requires a holistic approach that balances innovation, user experience, and sustainability. This not only leads to superior product design but also positions your hydraulic press as a leader in both industry functionality and market appeal, ensuring it stands out in a competitive landscape.