For enthusiasts and professionals in the automotive tool industry, the scissor car jack is a cornerstone of effective vehicle maintenance and repair. As one of the most frequently used tools, its design directly influences safety, efficiency, and ease of use. Understanding the ins and outs of scissor car jack design not only enhances your expertise in automotive equipment but also ensures trustworthiness in your recommendations and applications.
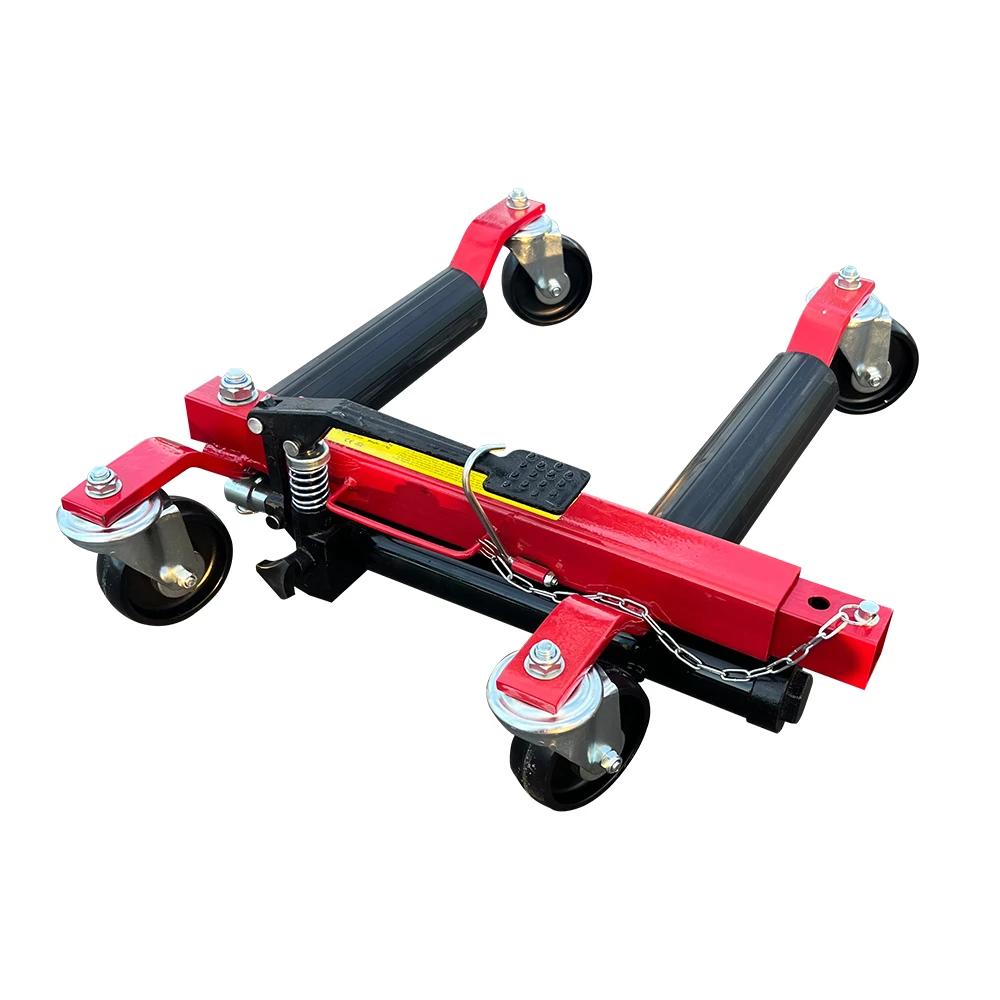
The scissor car jack is a mechanical system, primarily utilized to lift vehicles for tire changes or undercarriage repairs. Its design often includes two elongated arms that create a cross or scissor mechanism, allowing the device to expand and contract efficiently. The engineering behind this simple yet effective apparatus is rooted in mechanical advantage and load distribution principles, requiring precise calibration and high-quality materials.
The key component to consider in the design of a scissor car jack is its load capacity. Typically constructed from steel or aluminum alloys, these materials offer the necessary strength and durability while maintaining a manageable weight. For those aspiring to manufacture or improve upon existing designs, material selection is critical. High-carbon steel is commonly preferred for its excellent tensile strength, although newer models may incorporate reinforced aluminum alloys for a lighter alternative without sacrificing durability.
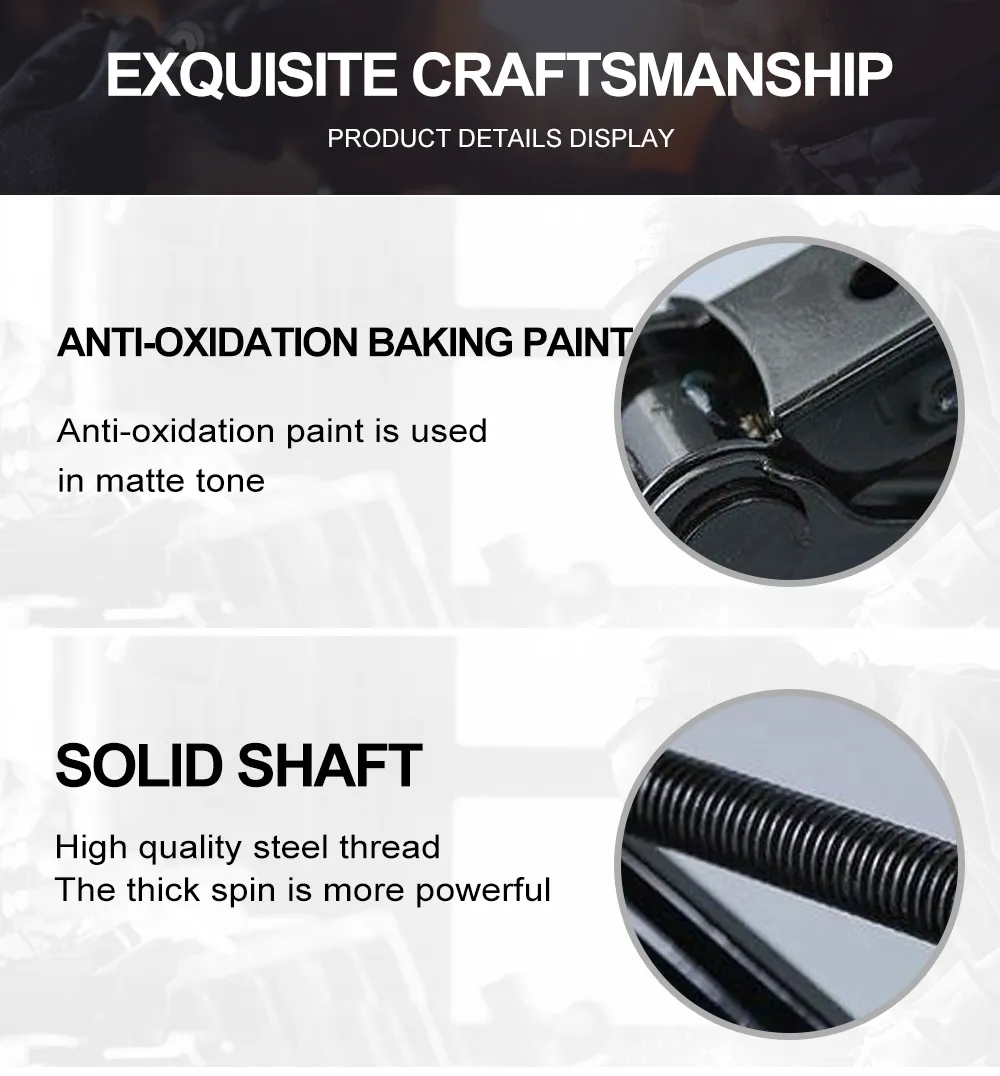
Ergonomics also play a significant role in the design of scissor car jacks. Modern designs strive to minimize user effort by optimizing handle length and grip design. A well-crafted handle not only ensures ease of operation but also reduces the risk of slippage during use. The angle of the crank handle is crucial—it should align with the user’s natural motion to minimize strain. Some advanced models even integrate ergonomic rotating handles that further enhance user experience by providing a more natural, fluid motion when lifting a vehicle.
scissor car jack design
Safety considerations are paramount in the design of all automotive lifting devices. For scissor car jacks, stability is enhanced through a wide base and a well-engineered pivot system that evenly distributes weight. An uneven load distribution can lead to potential hazards, making it essential for manufacturers to rigorously test their designs against various real-world scenarios. Anti-corrosion treatments are also vital, ensuring the longevity of the jack when exposed to harsh environments or extended periods of non-use.
Innovations in scissor jack design have led to several noteworthy advancements. The inclusion of electronic sensors is among the most exciting developments. These sensors can detect load imbalances or excess pressure, automatically halting the lifting process to prevent accidents. Another innovation is the introduction of hydraulic assistance in manual jacks, which significantly reduces the force required by the user and increases lifting speed.
Emphasizing the aspect of trustworthiness, it’s essential for consumers to seek certification from recognized safety standards organizations when purchasing a scissor car jack. Certification bodies like ASME (American Society of Mechanical Engineers) and ISO (International Organization for Standardization) provide rigorous testing and endorsement that assure a product meets high safety and performance standards.
In conclusion, the scissor car jack remains a critical tool in automotive maintenance, with its design continually evolving to meet the demands of safety, efficiency, and user-friendly operation. Whether you are enhancing an existing model or conceiving a new design, focusing on material quality, ergonomics, and safety innovations can significantly impact your success in the market. Ensuring your jack is tested and certified will further enhance its credibility, making it a reliable choice for consumers worldwide. By embracing these principles, professionals in the field can contribute to the ongoing advancement of this indispensable tool, driving innovation and trust in equal measure.