In the rapidly evolving landscape of automotive and industrial workshops, the shop press with gauge emerges as an indispensable tool, combining precision, efficiency, and reliability. As businesses and hobbyists alike continue to seek ways to improve accuracy and productivity, understanding the unique advantages of this equipment is paramount.
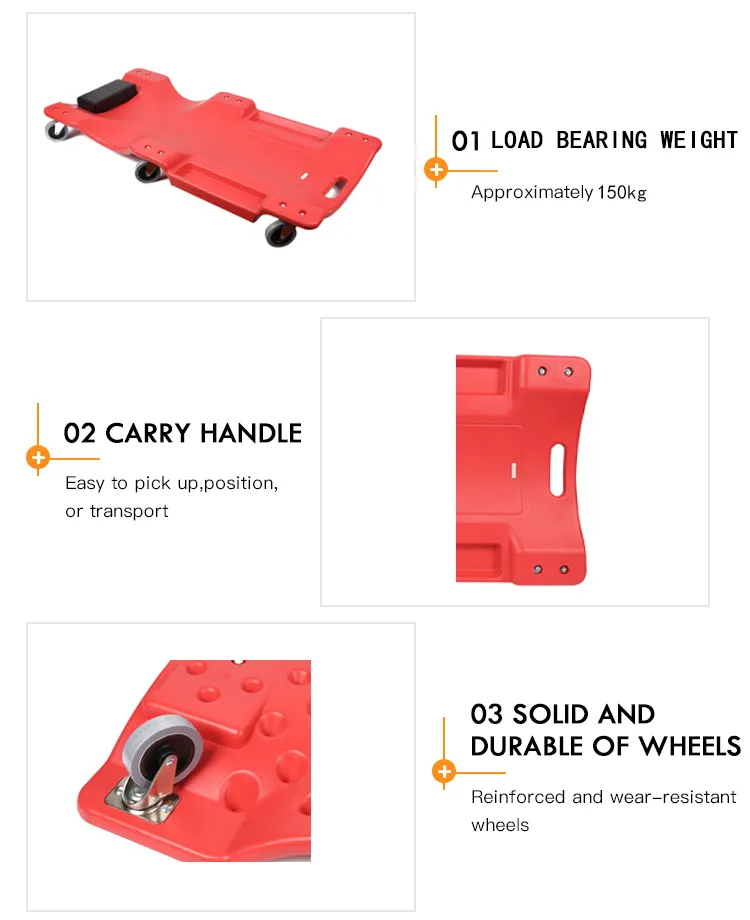
The shop press, fundamentally, functions to apply a controlled force onto an object, enabling tasks such as bending, straightening, or pressing bearings or bushings with unrivaled precision. The integration of a gauge in these presses adds an extra layer of sophistication, enabling operators to monitor and adjust the exerted forces with meticulous accuracy. This nuanced capability is particularly crucial in settings where precision is paramount — a small deviation can significantly impact the outcome of the task at hand.
Expertise in utilizing a shop press with a gauge comes with understanding the intricacies of pressure dynamics and the mechanical properties of different materials. Professionals in the field emphasize the importance of calibrating the gauge correctly and routinely, ensuring that the applied force remains consistent and true to the task's requirements. This practice not only enhances the quality of the output but also extends the longevity of the machinery, ultimately providing a better return on investment for businesses.
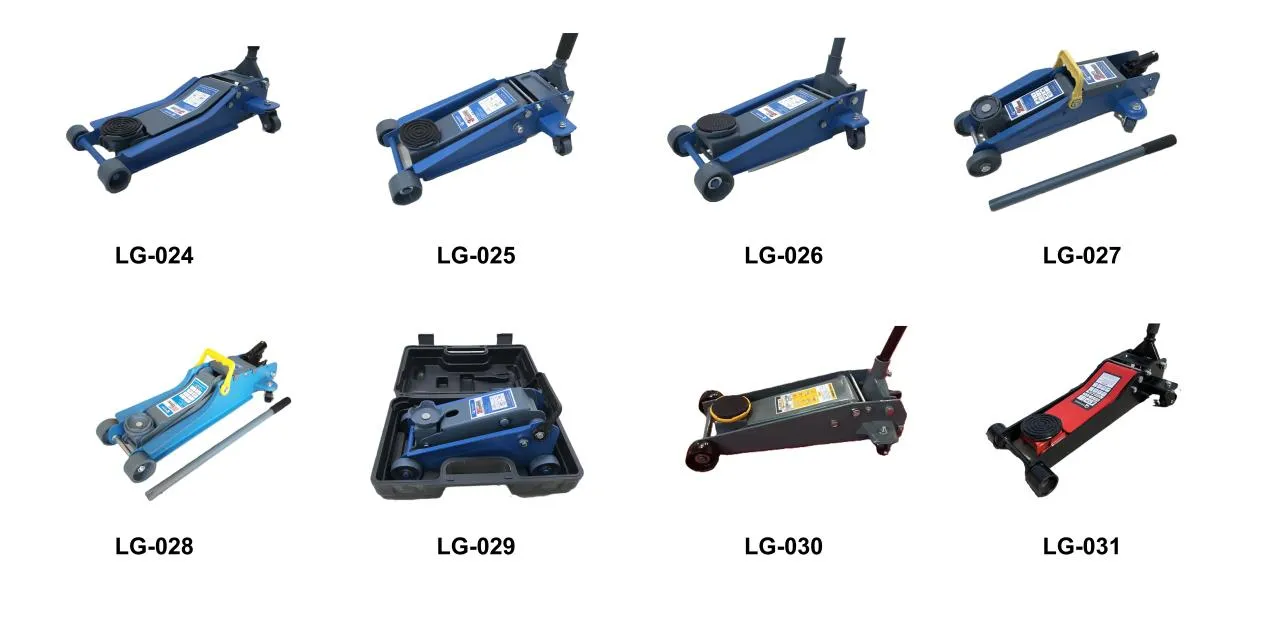
The authority of the shop press with gauge is well-documented in the testimonies of industry experts. Engineers and technicians extol the virtues of this tool in streamlining operations and minimizing human error. The ability to exert uniform pressure also reduces material wastage, contributing to a more sustainable and cost-effective operation. Moreover, the gauge enables the recording of pressure data, allowing for better control over the quality assurance process, a critical component in industries where standards are non-negotiable.
Trustworthiness in the operation of a shop press with gauge is rooted in the consistency it brings to the workshop. By offering a reliable measure of pressure, operators can undertake tasks with a confidence that manual systems or less sophisticated machinery cannot provide. This reliability is vital not only for the integrity of the machine components but also for the safety of the operators. In environments where heavy materials and significant forces are daily concerns, the safety provided by accurate pressure reading cannot be overstated.
shop press with gauge
One compelling feature of the shop press with gauge is its adaptability across various industries. From automotive to manufacturing, the versatility of this tool is showcased in its ability to switch seamlessly between tasks that demand different pressure settings and accuracy levels. For small business owners and hobbyists, this means investing in a single piece of equipment capable of performing numerous functions, offering a level of flexibility that few other machines can match.
To fully leverage the benefits of a shop press with gauge, users must consider the compatibility of the press with the tasks they regularly perform. Selecting a press with the appropriate tonnage for your most common applications ensures optimal performance and prevents overburdening the machinery, which can lead to premature wear or failure. Furthermore, understanding the specific functionalities of the gauge — such as its calibration options, measuring range, and display readability — further enhances its utility.
The shift towards machinery that combines tradition with technological advances is indicative of a broader trend aimed at improving work processes through innovation. Embracing tools that offer precise control over mechanical functions reflects a commitment to quality and efficiency. As more businesses recognize the advantages provided by incorporating a shop press with gauge into their operations, the focus naturally shifts towards optimizing its use through regular maintenance, training, and adherence to best practices.
In conclusion, the shop press with gauge stands as a testament to the need for precise, reliable, and versatile tools in the modern workshop. By equipping themselves with devices that marry traditional mechanical power with advanced monitoring capabilities, businesses and individuals can ensure high-quality results, safety, and longevity in their endeavors. Such tools not only enhance operational efficiency but also contribute significantly to the pursuit of excellence in any industry.