The hydraulic press has stood as an emblem of power and precision in the manufacturing and engineering sectors for decades. The workbench hydraulic press, a more compact adaptation of the traditional model, is engineered to offer flexibility and efficiency in modern workshops. This article delves deep into the capabilities, advantages, and specific applications of workbench hydraulic presses, ensuring buyers and users make informed decisions based on informed expertise.
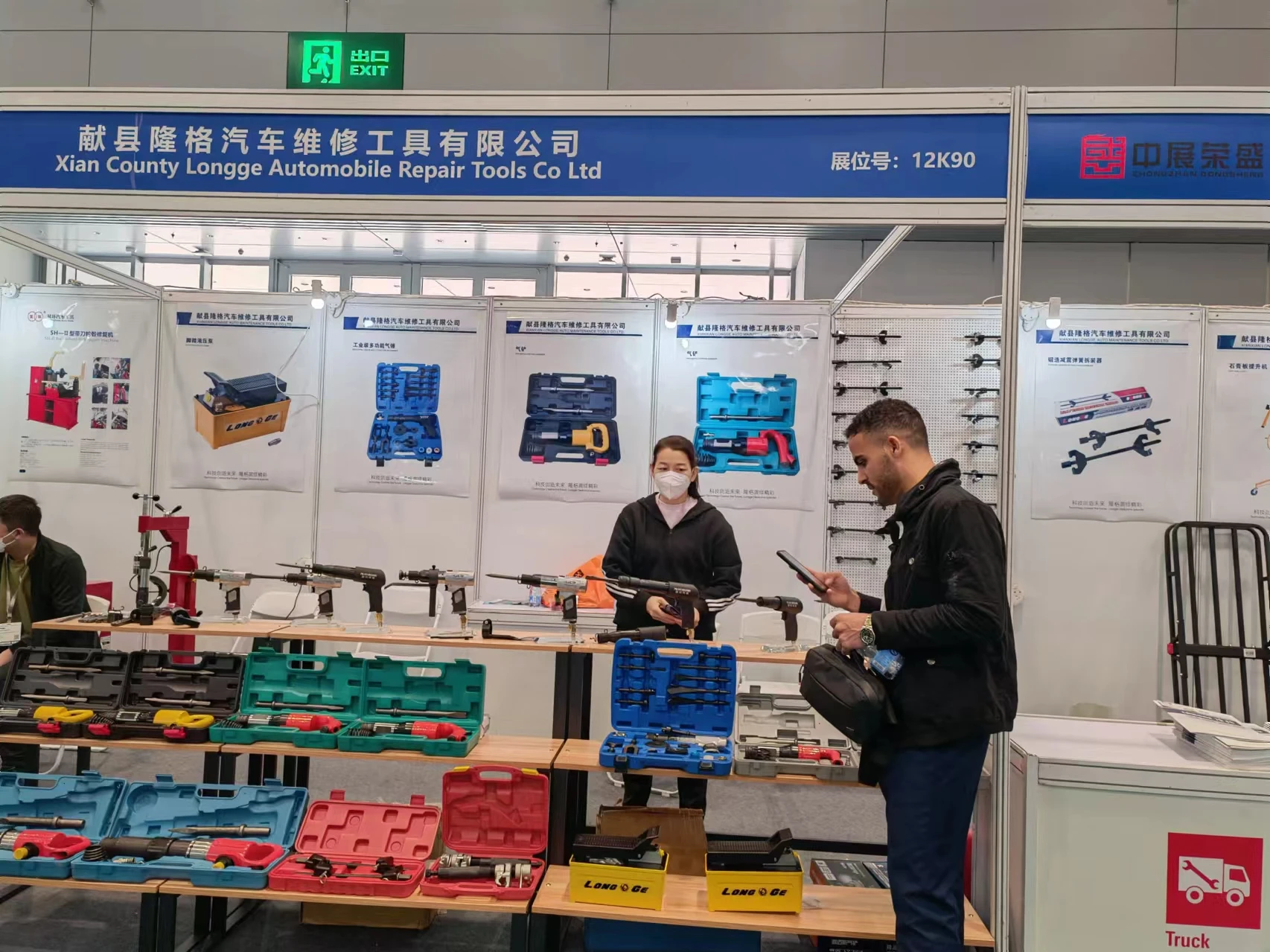
To begin with, the workbench hydraulic press is a pivotal tool designed for tasks that require precise application of force over a smaller surface area. These presses typically range from 1 ton to 30 tons of force, making them suitable for a variety of intricate tasks, from crafting delicate jewelry to fitting parts in a high-stakes automotive environment. The key to understanding the effectiveness of these presses is grasping the science of hydraulics—fluid mechanics enabling massive force multiplication through simple mechanisms, ensuring even small units can handle significant workloads.
A critical factor contributing to the unparalleled precision and power of a workbench hydraulic press is the quality of its construction. Manufacturers often use high-grade steel and cast iron, ensuring durability and stability. For instance, the cylinder used in these presses is typically crafted for high tension, ensuring zero leakage during operation, a hallmark of superior craftsmanship that elevates a brand’s authority within the market.
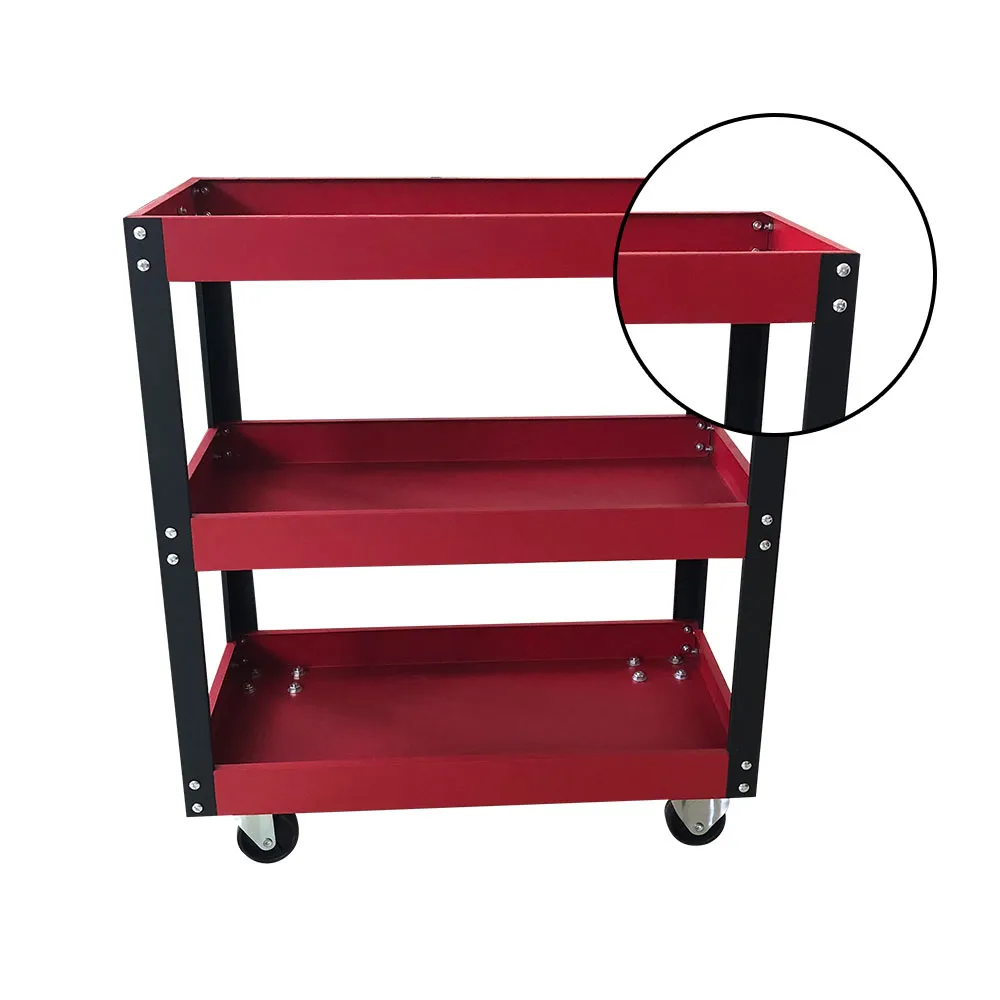
In exploring the expertise embedded in these tools, one must navigate the array of features offered. Adjustable pressure gauges and safety valves are now standard, allowing for user customization and security—preventing overloading and ensuring longevity. For enhanced usability, many modern models come equipped with digital controls, facilitating ease of operation and a heightened level of precision that is essential in industries such as aerospace and electronics manufacturing.
Among professionals, there is a shared trust in brands that consistently deliver quality. Trustworthiness in the realm of hydraulic presses translates to reputation, service, and support that one can rely on. Brands that provide extended warranties and user support, encompassing not only the initial setup but training and long-term maintenance, often stand out.
workbench hydraulic press
Navigating the extensive array of hydraulic presses can be daunting, particularly when specificity of task is at play.
The workbench model’s real-world applications are expansive. For instance, in the automotive sector, these presses facilitate the installation of bearings and bushings—tasks requiring precision but also repeated force. In a completely different arena, jewelers utilize these presses for metal forming or precision cutting, where the stable, consistent application of pressure results in unparalleled craftsmanship.
Adopting a user-centric approach in examining these machines reveals insights into the hands-on experience of operators. This ensures that a workbench hydraulic press not only fits within the desired parameters of force and size but also provides comfort and ease of use. Ergonomic designs, such as height-adjustable platforms and intuitive control interfaces, redefine user experiences, transforming a complex task into a streamlined process.
The decision to integrate a workbench hydraulic press into a production line or workshop is an investment—a commitment to efficiency and precision. Understanding the specific needs of the task at hand is critical. This involves assessing the necessary force, desired precision, and available workspace. Consultations with experts, reviews of leading brands, and trial runs are advisable steps to confirm that the selection meets operational demands and enhances productivity.
In conclusion, the world of workbench hydraulic presses combines the best of industrial capability with practicality and user-friendly design, embodying efficiency and reliability. Their versatility and precision align with an impressive range of industries, making them a dynamic component of any modern workshop. When embraced fully, these machines are not just tools; they are transformative forces of productivity, expertise, and unparalleled accuracy in an ever-evolving manufacturing landscape.