When selecting a manual shop press, understanding the intricacies and mechanics can significantly enhance workshop operations. This tool, although simple in design, holds the power to transform mundane tasks into efficient processes. With a focus on experience, expertise, authority, and trustworthiness, this article delves into what makes a manual shop press indispensable for professionals and enthusiasts alike.
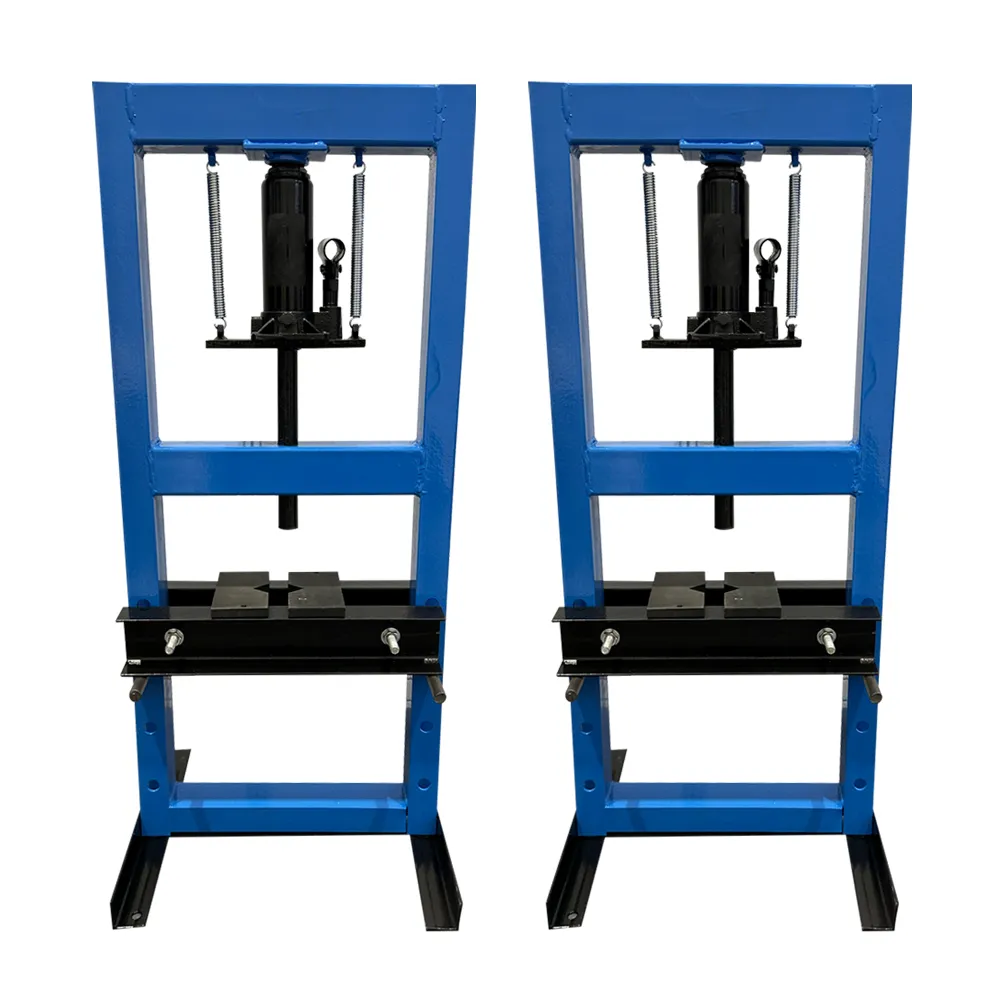
A manual shop press implements a hydraulic or screw design to generate immense pressure, allowing users to perform tasks such as bending, shaping, and pressing metal with remarkable precision. The simplicity of manual operation belies the nuanced expertise required to fully exploit its capabilities. From automotive workshops to metal fabrication units, its versatility is unmatched, offering applications ranging from pressing bearings to straightening bent components.
Leverage stems from understanding its construction and functionality. Typically, a robust frame, a ram for applying pressure, and a bed to hold the workpiece compose a manual shop press. Material choice influences durability and performance; thus, selecting presses with high-quality steel frames is critical for professional resilience. Capacity varies, often between 6-50 tons, aligning with user needs and specific workshop applications.
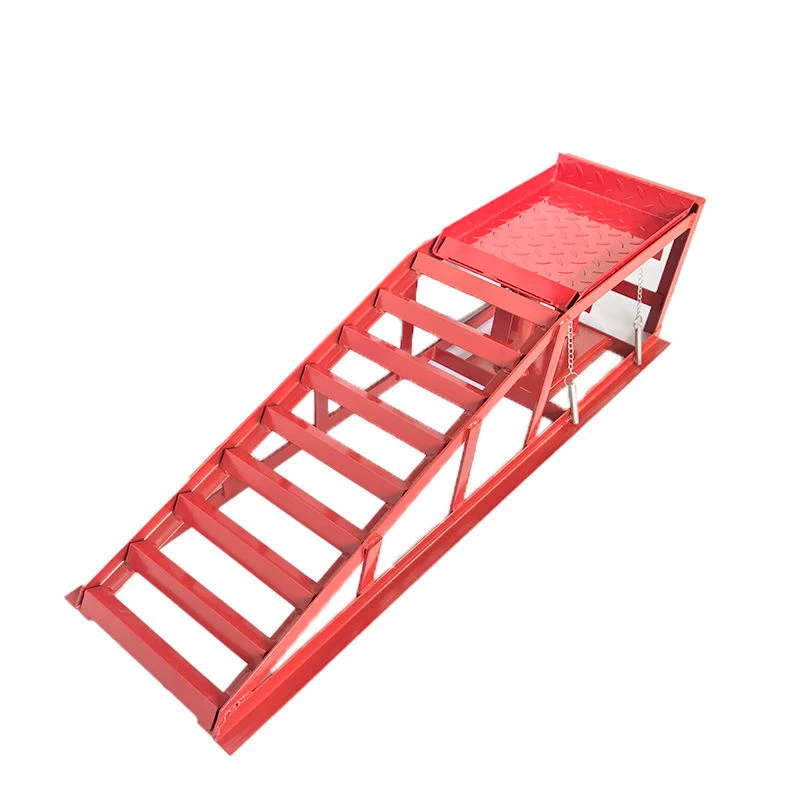
The manual shop press commands authority through its sheer force, yet mastering it involves nuanced craftsmanship. A seasoned professional approaches each press job with an understanding of the unique pressures involved, precisely calculating the needed force to avoid damaging materials. For instance, adjusting the ram speed and monitoring the pressing cycle becomes second nature to the experienced user, vital for tasks such as pressing bushings or straightening shafts.
Equally important is the skill of maintenance. Regularly inspecting for wear or fatigue in the frame or hydraulic components ensures the tool's reliability and extends its lifespan. Knowledgeable users are keener to identify signs of oil leaks or misalignments that could compromise safety or efficiency.
manual shop press
From an authoritative standpoint, brands like Blackhawk, Sunex, and OTC have set benchmarks with their reliability and innovation in manual shop presses. Reviews highlight their durability and value, creating a trust fabric among professionals. The endorsement of such brands speaks volumes about product reliability, influencing buyer decisions significantly.
Trustworthiness in manual shop presses is woven through user testimonials and professional endorsements. Users consistently extoll the tool's safety features, such as dual-speed control for the hydraulic ram or safety pins for bed adjustments, which prevent accidental overloads. The capacity to handle demanding tasks without malfunction instills confidence, pivotal for operations where precision is paramount.
Especially in automotive repair, where the demands can fluctuate, having a reliable manual press ensures tasks are completed without delay, bolstering productivity. Workshops aiming to optimize space find manual shop presses advantageous due to their compact footprint, marrying power and efficiency without necessitating expansive floor space.
Adapting to specific tasks further amplifies its utility; customizable attachments can transform a standard press into specialized equipment, like a brake drum press, thereby enhancing its value proposition. This adaptability means that manual shop presses remain an enduring choice for both burgeoning DIY enthusiasts and seasoned industry professionals.
Navigating the choice and operation of manual shop presses from an informed perspective undeniably confers efficiency, resilience, and satisfaction in various tasks. Whether embarking on intricate metalwork projects or routine automotive repairs, the insights offered by experienced users provide a roadmap to maximizing the potential of this invaluable workshop tool.