Navigating the Essentials of a Machine Shop Drill Press A Comprehensive Insight
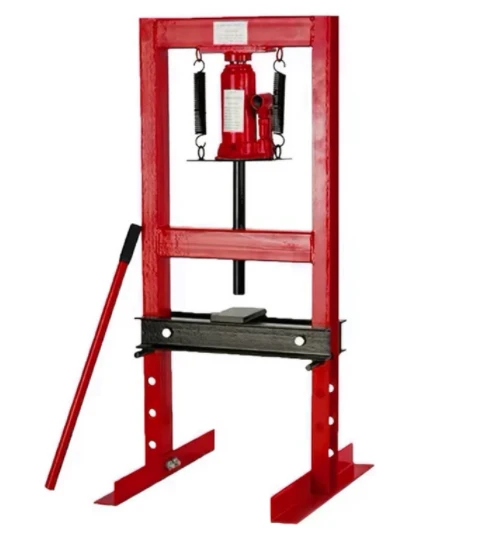
In the intricate realm of metalworking and fabrication, a machine shop drill press stands as a cornerstone of precise machining, bringing both versatility and efficiency to workshops worldwide. As an experienced practitioner in the field, I am excited to share a detailed exploration of this crucial tool that elevates machining precision to an art form. With its ability to bore holes with unparalleled accuracy, the drill press is an indispensable asset, and understanding its intricacies can significantly enhance productivity and output quality.
At its core, a drill press is engineered to deliver vertical drilling capabilities, ensuring that holes bored into materials maintain consistent angles and depths. Its design facilitates a controlled environment where high-tolerance work can be consistently performed, making it a quintessential machine in both small-scale artisan settings and large-scale industrial shops. The robust frame of a drill press, coupled with its adjustable components, allows artisans and technicians alike to fine-tune operations, ensuring that every drill is executed with precision.
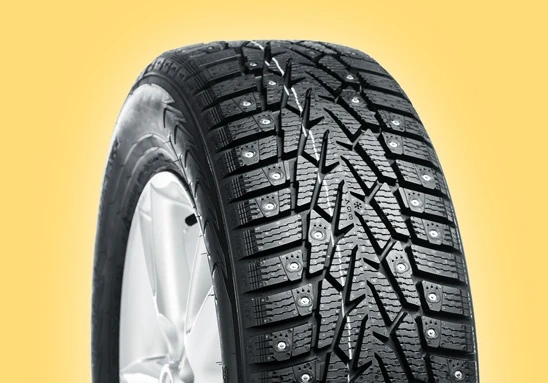
From a professional standpoint, the key features of a machine shop drill press underline its proficiency. One of the standout attributes is the adjustable spindle speed. A variable speed control allows for customization based on material type, ensuring optimal results across diverse projects. This adaptability not only enhances the drill's performance but also prolongs its lifespan by reducing unnecessary strain on its components.
The drill press's quill assembly is another component worth noting. It provides controlled axial motion, which is imperative for delivering accurately bored holes. With advanced models featuring depth stops, operators can achieve consistent and repeatable results without the constant need for recalibration. This assembly, coupled with a reliable feed lever system, makes the drill press a user-friendly tool that emphasizes both safety and productivity.
Material clamping systems in modern drill presses offer a refined approach to securing workpieces. The inclusion of vises and clamps that are designed to hold a variety of shapes provides the operator the confidence to undertake intricate tasks without the concern of workpiece slippage. This feature is especially crucial when handling irregularly shaped materials or drilling at non-standard angles.
machine shop drill press
Furthermore,
advancements in digital readouts have enhanced the precision of drill presses exponentially. These devices enable operators to precisely monitor spindle depth and position, eliminating the guesswork traditionally associated with analog gauges. This innovation, combined with modern laser guidance systems, ensures that even novice operators can achieve professional-grade results.
While the physical aspects of a drill press are undeniably essential, understanding how to maintain and operate these machines efficiently is equally critical. Regular maintenance, including lubrication of moving parts and timely replacement of worn components such as belts or bearings, ensures the drill press remains an enduring part of the machine shop arsenal. Maintaining sharp drill bits and using the appropriate bit for each application further extends the machine's life and optimizes output.
When considering the purchase of a machine shop drill press, evaluating the machine's horsepower and maximum spindle travel is vital. These specifications dictate the press's ability to handle heavier, thicker materials and impact the overall versatility of the unit. Professional reviews and recommendations, based on real-world testing, can significantly aid in this decision-making process.
It's also worthwhile to consider the drill press's warranty and the manufacturer's support network. A comprehensive warranty can serve as a testament to the manufacturer's confidence in their product, while an established support network ensures that any operational challenges can be swiftly addressed.
In conclusion, a drill press is more than just a simple tool; it is a sophisticated machine that combines precision engineering with innovative features to create a powerhouse of productivity in any machine shop. Understanding its components and functionalities, and maintaining a routine of regular care, not only enhances its performance but also solidifies its role as a keystone of modern machining practices. Whether you are a seasoned technician or new to the world of fabrication, mastering the drill press's capabilities unlocks a pathway to superior craftsmanship and high-quality production.