Building a shop press can be a transformative project for anyone interested in enhancing their workshop capabilities. The process, though intricate, offers a rewarding experience packed with valuable insights and tangible results. A shop press serves as an indispensable tool, particularly for those who frequently engage in tasks like metal forming, bearing installation, or any activity requiring substantial compressive force. By fabricating your own, you not only save on costs but also gain the flexibility to customize it to specific needs, resulting in a more personalized and efficient workshop tool.
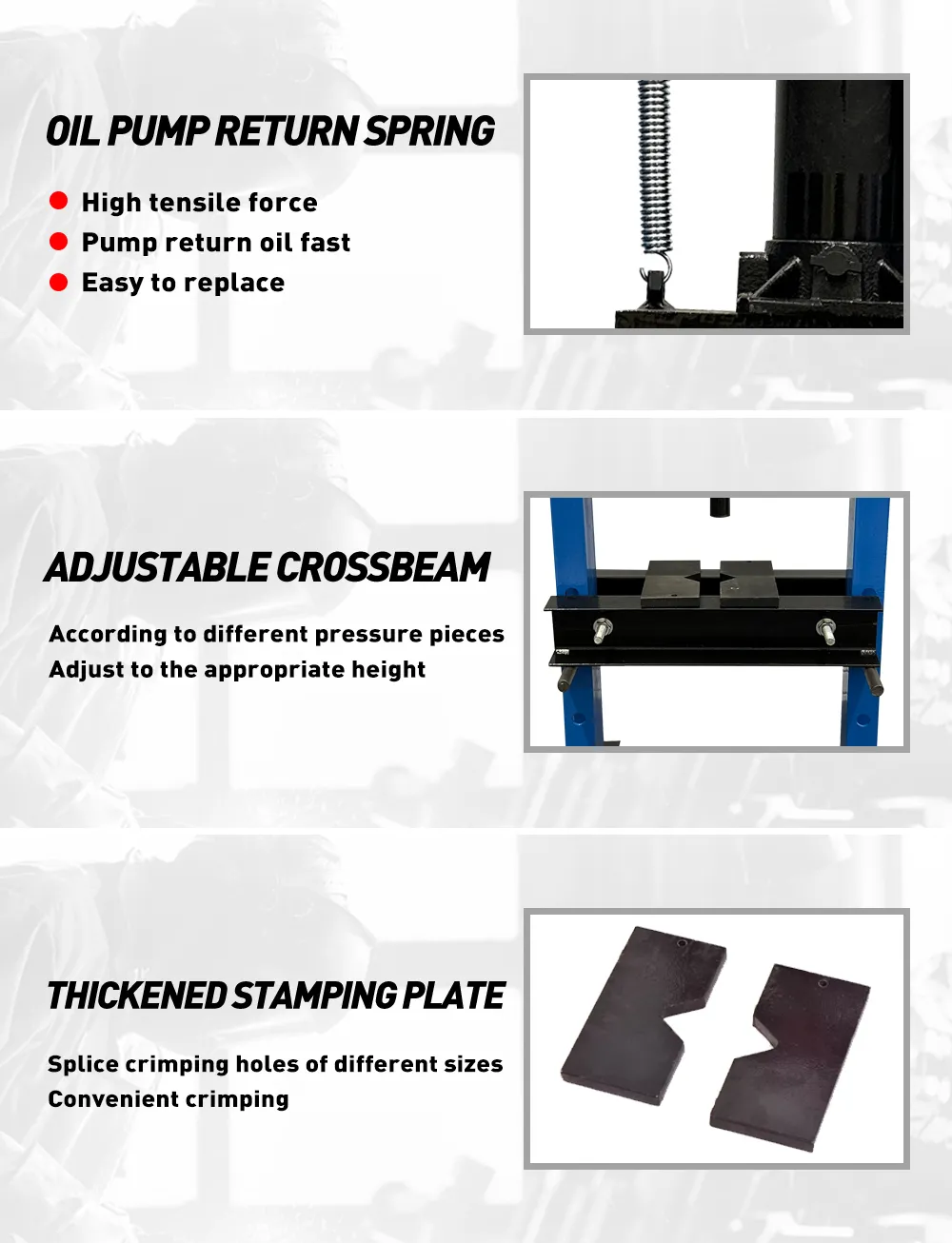
The foundation of a successful shop press construction begins with selecting high-quality materials. Expertise in material selection is crucial; opting for robust steel ensures durability and longevity. Mild steel is often preferred due to its balance of strength, affordability, and ease of welding. Additionally, hydraulic components are at the core of the pressing mechanism. A hydraulic bottle jack, available in various capacities from 12 to 50 tons, typically serves as the power source. When selecting the jack, it's essential to assess the maximum force you'll need, as underestimating this could limit the press's functionality.
Precision in the design phase cannot be overstated. A critical aspect is determining the size of the press frame, which should align with the space available in your workshop and the size of the projects you'll be handling. The same meticulous attention should apply to the assembly of the frame. Rigorous measurements and cuts ensure that all components fit together seamlessly, maintaining structural integrity. Welds must be strong and clean, capable of withstanding the high pressures exerted during operation.
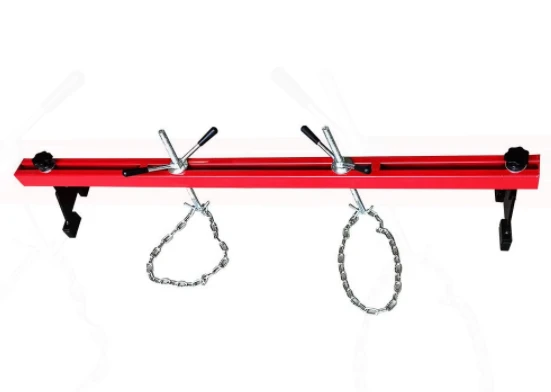
Trustworthiness and safety are paramount. Incorporating safety features, such as pressure relief valves and safety pins, can prevent accidents, offering peace of mind during use. A reliable shop press must undergo stringent testing before regular operation; it should demonstrate stability and resilience under load without showing signs of stress or misalignment.
building a shop press
While building a shop press from scratch is an admirable endeavor, it is important to acknowledge the intricate skill set required. Prior welding experience and familiarity with hydraulic systems are valuable expertise areas that can significantly simplify the process. Consulting with seasoned professionals or referencing authoritative guides can further enhance the quality and safety of your final product.
Beyond the technical construction, understanding shop press functionalities enhances user experience and project outcome. Shop presses are versatile, ideal for tasks that involve pressing, straightening, or bending metals. For advanced users, integrating a pressure gauge can optimize precision in these applications, enabling more nuanced control over the force applied.
The journey of constructing a shop press exemplifies the confluence of skill, precision, and creativity. Each element, from material selection and design to implementation and testing, plays a critical role in the final product's success. This project is not just about creating a tool but crafting an invaluable asset that empowers your workshop activities and enhances project results.
Engaging with this process equips you with profound knowledge and hands-on experience, reinforcing your workshop's efficiency and capability. The time and effort invested yield significant returns, solidifying your understanding of mechanical dynamics and tool fabrication. This expertise not only enhances your repertoire but also elevates your authority and credibility in the realm of metalworking and tool production, giving you a competitive advantage in executing complex projects with confidence and precision.