Understanding the intricacies of a press shop machine can be the key to optimizing production efficiency and ensuring superior quality in metal forming processes. A well-selected machine not only accelerates manufacturing but also minimizes errors, offering businesses a competitive advantage.
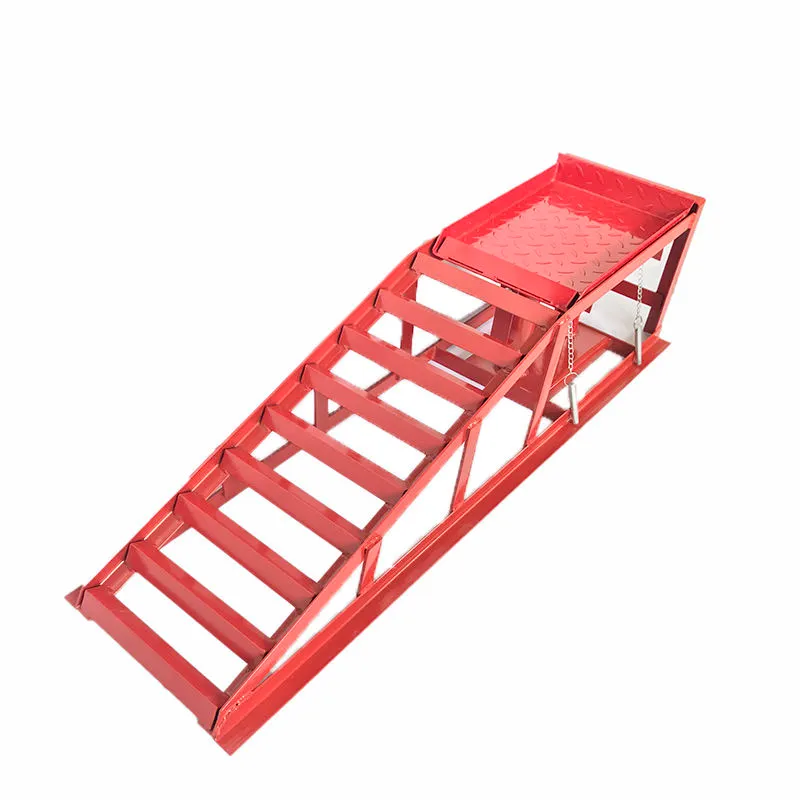
Press shop machines, pivotal in automotive and appliance industries, are designed to transform flat sheet metals into complex shapes through stamping, punching, bending, or forming. To truly grasp the significance of these machines, comprehensive knowledge of their workings and applications is indispensable.
Press shop machines come in various types, each catering to specific manufacturing needs. Hydraulic presses utilize a hydraulic cylinder to generate compressive force. They are known for their precision and ability to manage complex jobs and materials with varied thickness. Mechanical presses, driven by mechanical components, are celebrated for their speed and productivity, making them ideal for high-volume production runs. Pneumatic presses, while less common, offer rapid cycling times and are favored for certain niche applications where speed and cost-efficiency are paramount.
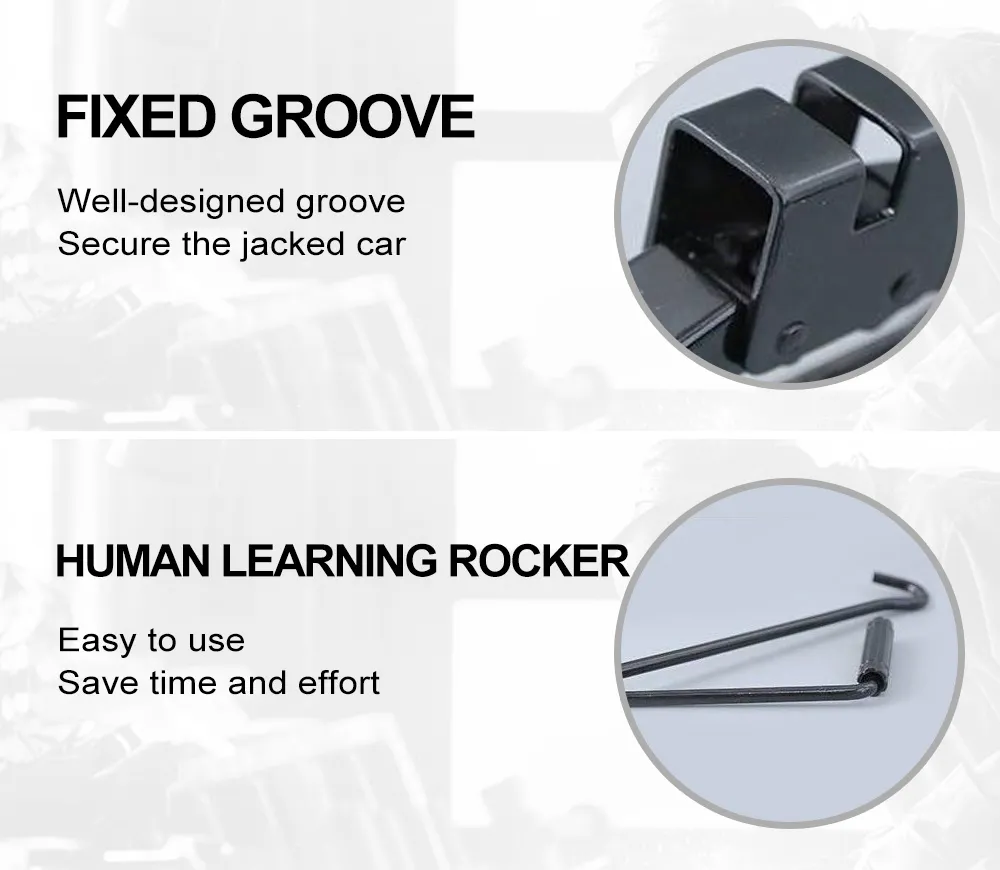
Selecting the appropriate press shop machine hinges on understanding the specific requirements of the task at hand. Factors such as production volume, material type, and desired accuracy must guide the decision-making process. For instance, high-volume operations may benefit from mechanical presses due to their unmatched speed, whereas tasks demanding acute precision might better align with a hydraulic press.
Ensuring that the machine is properly maintained is critical for maintaining its efficiency and longevity. Regular inspections and timely servicing can preempt mechanical failures, ensuring uninterrupted operations. Achieving optimal performance involves not only the acquisition of the appropriate machine but also the employment of skilled operators who can maneuver the equipment with expertise. Well-trained staff can significantly reduce material wastage and operational downtime, which translates into cost savings.
press shop machine
Integrating cutting-edge automation technology can further revolutionize a press shop. The use of sensor systems within press shop machines enhances safety and precision by instantly detecting and relaying operational anomalies. Automation reduces human error and increases repeatability, providing a pathway to consistent product quality and improved throughput rates.
The credibility of press shop machine manufacturers also bears consideration. Opting for machines from reputable brands ensures reliability, quality customer support, and better access to spare parts. Manufacturers with proven track records often provide resources for training and technical support, which augments the trustworthiness of their products in an industry where precision is paramount.
Compliance with safety standards cannot be overstated. The sensitive nature of press machine operations necessitates rigorously adhering to occupational safety protocols. Ensuring machine setup conforms to these standards not only safeguards operators but also maintains the company’s reputation by avoiding costly legal ramifications from potential workplace incidents.
For businesses keen on keeping pace with evolving technologies, keeping abreast of industry innovations is vital. Engaging with industry publications, technology expos, and seminars provides invaluable insights into emerging trends and technologies that could innovate traditional methodologies. As the model of Industry 4.0 gains traction, the convergence of IoT (Internet of Things) and press shop machines promises smarter operations and data-driven decision-making.
A strategic investment in the right press shop machine, underpinned by expertise and sustained by judicious maintenance practices, can significantly influence a manufacturer's standing in an intensely competitive market. By leveraging expert guidance, robust technology, and unwavering commitment to quality, businesses can harness press shop machines to elevate operational performance and secure a sustainable edge over their competitors.