Pneumatic hydraulic shop presses are indispensable tools in various automotive, manufacturing, and engineering industries. They are essential for tasks that require high-force applications, such as pressing, bending, and forming materials. Understanding their intricate design and functionality can elevate a professional's ability to optimize their use effectively.
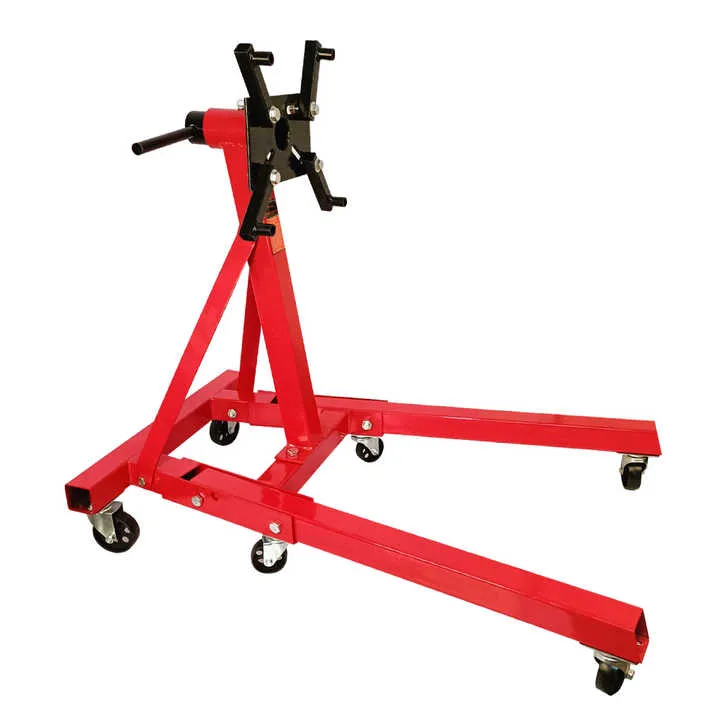
A pneumatic hydraulic shop press combines the power of both pneumatic and hydraulic systems. While they might seem similar, pneumatic components operate with air pressure, offering smoother, faster operations. On the other hand, hydraulic systems utilize liquid power, typically oil, known for delivering substantial force with precision. By integrating these systems, users benefit from both speed and strength, making it a versatile asset in any workshop.
The practical experience of working with a pneumatic hydraulic shop press underlines its efficiency and sheer power. For instance, a professional automotive repair specialist might use this press to remove or install bearings and bushings. The pneumatic system allows for quick, smooth movement, positioning the material accurately. Once in place, the hydraulic system engages, applying the needed force steadily without risk of overextension or material damage. The dual-system design minimizes manual effort, reduces operation time, and enhances safety, a critical factor in environments where precision and reliability are non-negotiable.
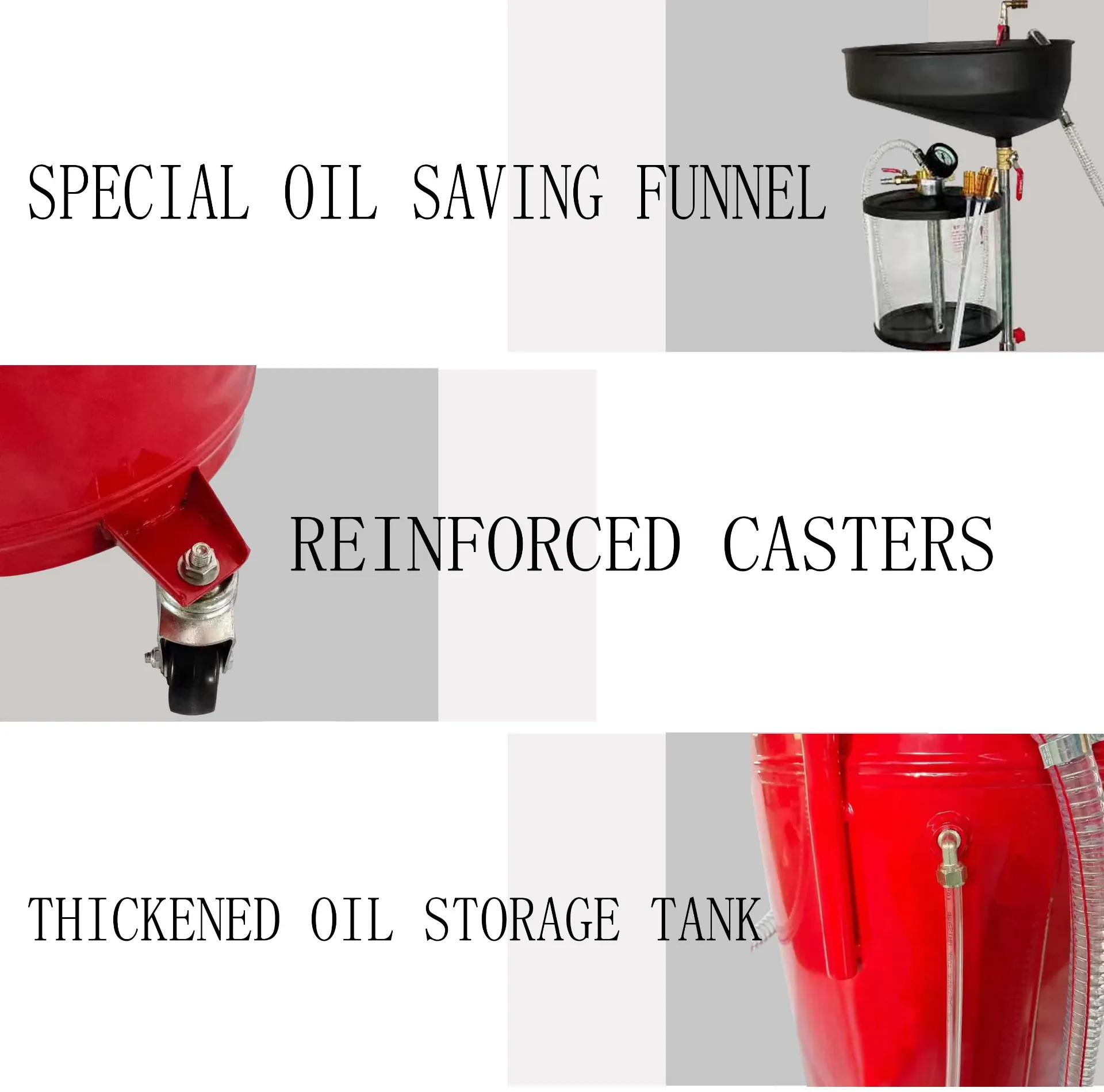
From an expertise viewpoint, the construction of these presses is meticulous. They typically come equipped with a durable steel frame to withstand extreme pressures and prevent deformation. The hydraulic component often features a piston-cylinder mechanism capable of withstanding thousands of pounds of force. Proper maintenance is central to ensuring longevity—regularly checking for air leaks in the pneumatic system or inspecting hydraulic oil levels can prevent operational deviations or mechanical failure.
pneumatic hydraulic shop press
Trustworthiness in a pneumatic hydraulic shop press is further anchored by industry standards and certifications. Reputable manufacturers subject their products to rigorous testing, ensuring compliance with safety norms such as OSHA or ANSI standards. These quality assurances provide users with the confidence that the press will perform reliably even under demanding conditions.
Authoritativeness comes from understanding the nuances of selecting the right model for specific applications. Factors like the tonnage capacity determine the maximum force the press can exert. Professionals recommend choosing a press with a capacity slightly above the maximum required for your tasks to prevent overloading and maintain operational efficiency. Moreover, additional features such as pressure gauges, safety valves, and adjustable tables can enhance functionality and user safety, providing a more controlled environment for various applications.
In conclusion, a pneumatic hydraulic shop press represents a sophisticated synergy between hydraulic strength and pneumatic speed. As machinery technology advances, these presses are continually refined to offer even greater precision, reliability, and ease of use. Mastery of these tools, backed by practical experience, technical expertise, and industry-backed reliability, underscores their irreplaceable role in modern industrial processes. Whether refining processes, enhancing productivity, or ensuring safety, investing in a top-quality pneumatic hydraulic shop press is an enduring choice for any serious professional or business.