Shop press tools are indispensable assets in professional and DIY automotive repair and metalworking workshops. Renowned for their efficiency in pressing, bending, and straightening tasks, these tools are essential for anyone looking to enhance their workshop capabilities. Understanding the nuances of shop press tools can substantially elevate your project's success and reliability.
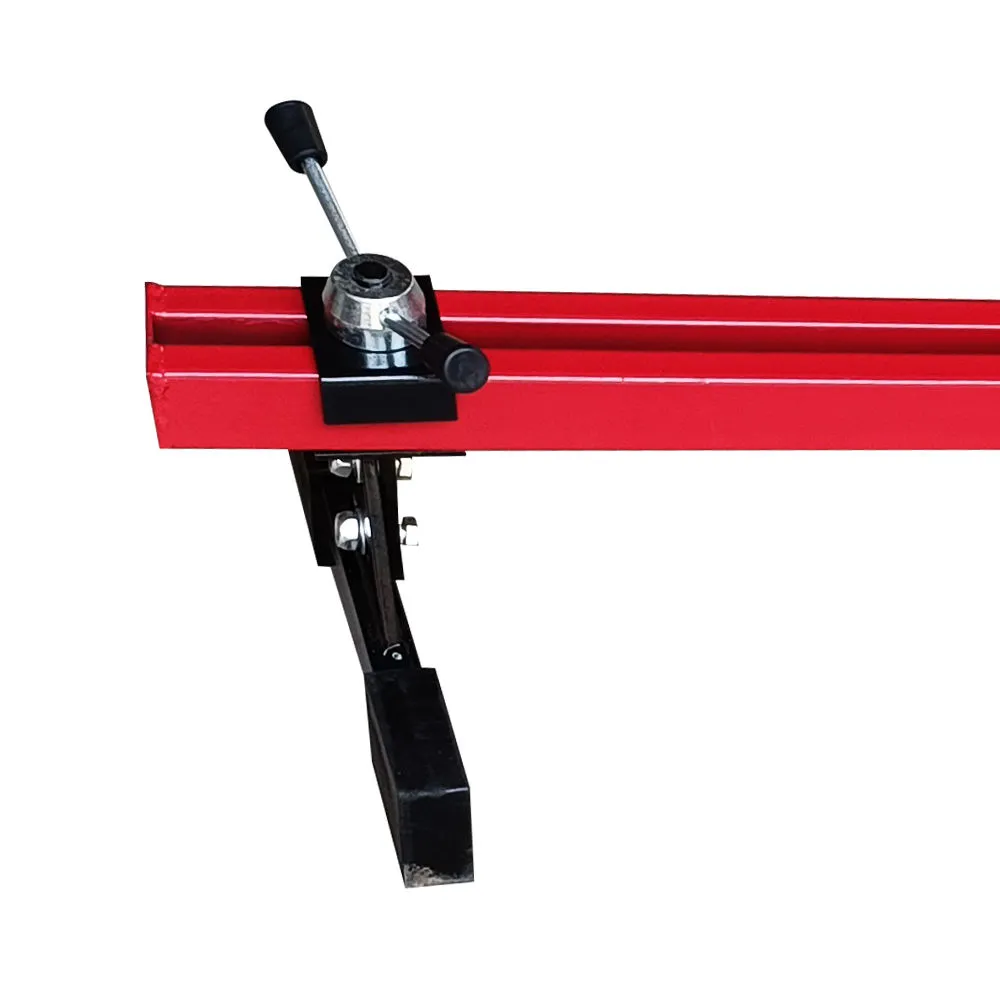
At the heart of shop presses is their ability to generate high levels of force to manipulate materials with precision. Whether conducting a straightforward wheel bearing replacement or tackling complex chassis fabrication, a suitably powerful shop press makes all the difference. These tools are available in various configurations and capacities, typically ranging from six tons to over fifty tons. Selecting the appropriate capacity revolves around the specific demands of your projects; inadequate capacity can lead to unsatisfactory results or equipment damage.
The hydraulic shop press, preferred by many professionals, offers unparalleled control and power. The hydraulic mechanism typically involves using a pump—manual, air, or electric—to create immense pressure with minimal human effort. Unlike mechanical alternatives, hydraulic presses provide smoother operation and a finer range of motion, essential for delicately calibrated tasks.
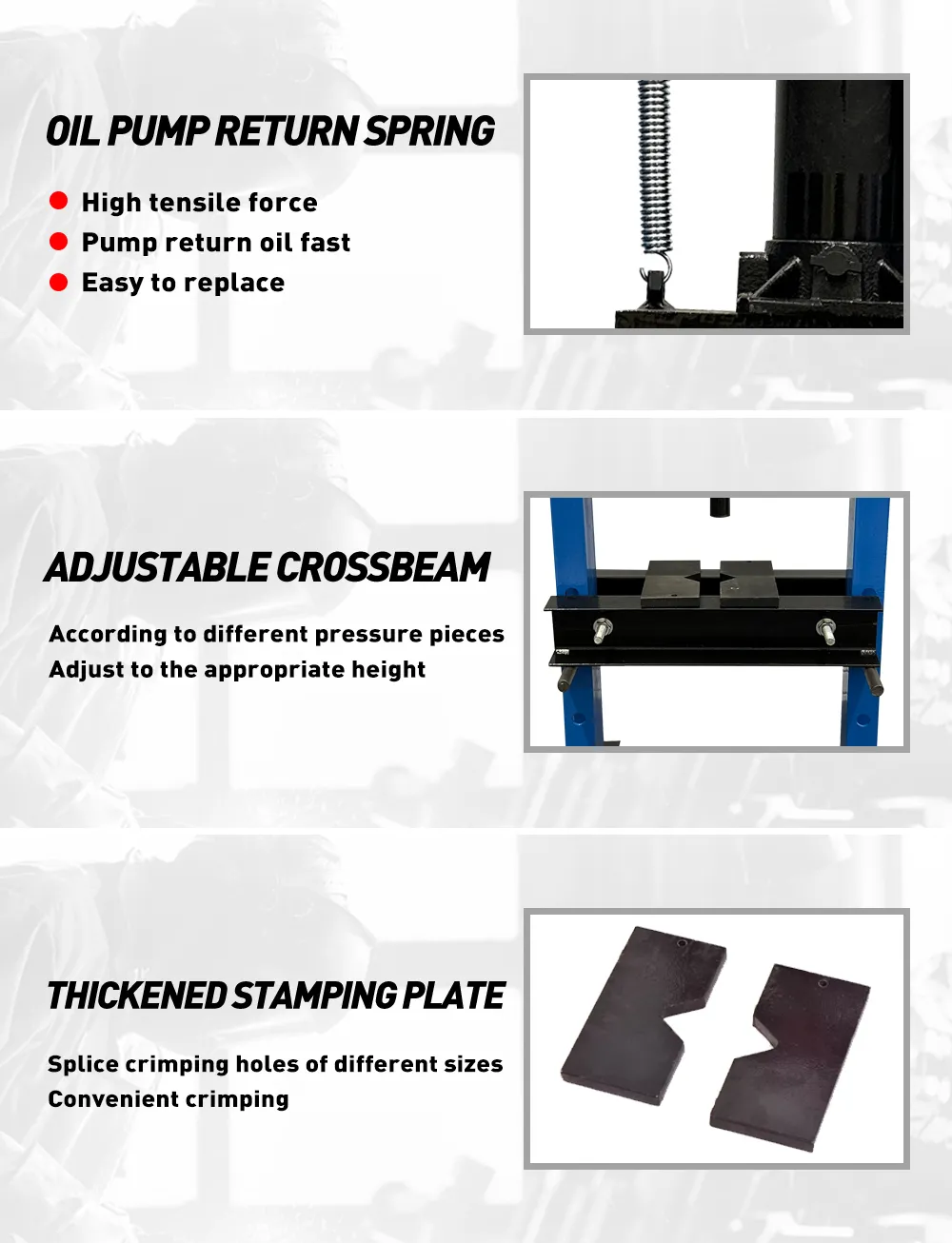
When it comes to specialization, bearing pressing stands out as one of the primary applications. Proper installation and removal of bearings are crucial for the longevity and performance of automotive systems, and shop presses deliver the precision required to avoid damage. Beyond bearings, these presses deftly handle tasks involving U-joints and bushings, underscoring their versatility.
For enthusiasts and professionals inclined towards metal fabrication, these presses also facilitate tasks like bending and forming metal parts. This capability allows for custom metalwork, essential in restoration projects or creating bespoke automotive components without necessitating multiple specialized machines.
shop press tools
An often overlooked but critical aspect of shop press tools is their role in enhancing workshop safety. By automating force application, they significantly reduce the physical strain on mechanics and technicians. This not only leads to more accurate outcomes but also protects operators from musculoskeletal injuries associated with manual exertion.
Investing in a high-quality shop press can transform operational efficiency and precision, yet it's equally crucial to consider the tool's durability and serviceability. Reputable brands offer robust designs made from industrial-grade materials that withstand frequent use. Maintenance also plays a pivotal role in longevity; periodic checks on the hydraulic system, ensuring airtight seals and lubricated components, prevent costly downtimes.
Expertise in utilizing shop press tools increases their value exponentially. Training and experience refine operators' abilities to execute projects swiftly while maintaining exceptional quality. Thus, professionals must prioritize familiarizing themselves with different setups and operation methods to exploit their full potential.
Lastly, building trustworthiness around your projects involves using verified equipment from reputable manufacturers. Certifications and adherence to safety standards reassure clients of your commitment to quality and safety, enhancing your workshop's reputation.
In conclusion, shop press tools are more than just mechanical instruments. They are cornerstones of efficiency, safety, and precision in metalworking and automotive repair. By understanding their applications, maintaining them diligently, and enhancing user expertise, these tools significantly boost both the quality and credibility of any workshop undertaking.