For professionals seeking efficiency and precision in maintenance or fabrication tasks, the importance of a reliable hydraulic shop press cannot be overstated. At the heart of many workshops lies the 10-ton hydraulic shop press, a quintessential tool that embodies strength, versatility, and efficiency. This write-up delves deep into its practical applications, expert insights, and essential tips for maximizing its utility while underscoring the attributes of experience, expertise, authoritativeness, and trustworthiness.
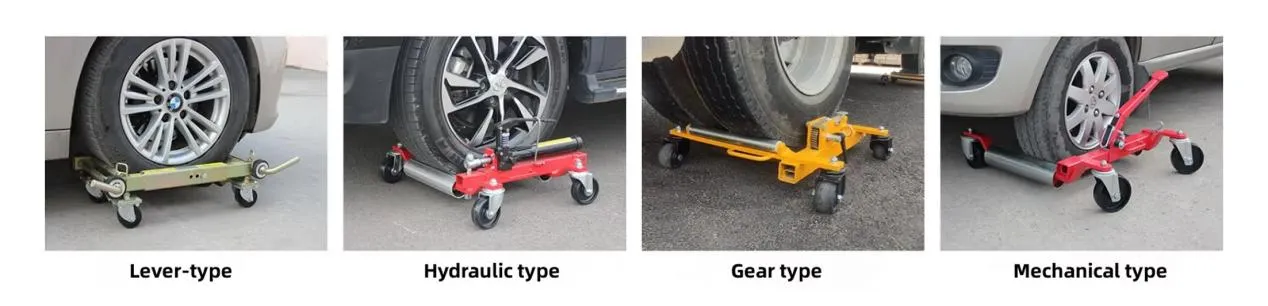
The 10-ton hydraulic shop press is indispensable in any environment where heavy-duty material manipulation is required. From automotive workshops to metalworking shops, this equipment is designed to deliver results with precision. Its ability to exert a force of up to 10 tons makes it ideal for pressing, bending, and straightening tasks, facilitating the work of professionals across various industries.
Fundamentally, the use of a 10-ton shop press starts with understanding its key components and operation. The primary assembly includes a hydraulic cylinder, a bed frame, and a pump. Expert operators know the pressing capability depends largely on the efficiency of the hydraulic system, thus regular maintenance checks for oil levels and potential leaks are crucial. A pristine hydraulic system ensures consistent pressure application, which is central to achieving optimal performance.
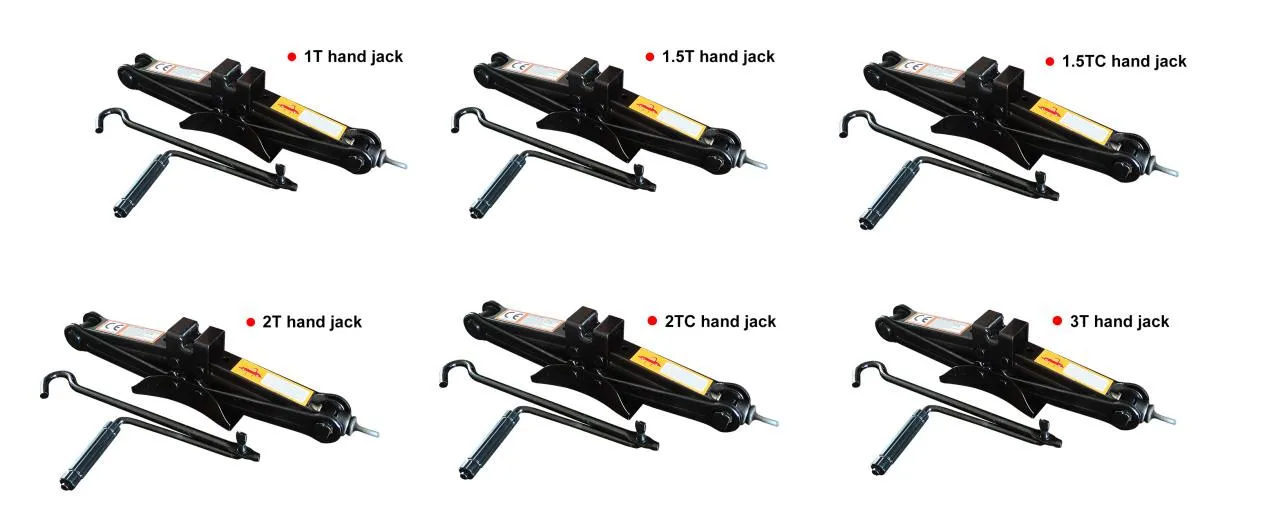
In automotive settings, a 10-ton press is a go-to tool for removing and installing bearings, bushings, and gears. Its ability to apply uniform pressure ensures these components fit perfectly without damage. Experienced technicians often highlight the press's utility in straightening bent components, a task that manual labor cannot achieve with the same precision or safety.
Metalworkers find the 10-ton hydraulic shop press invaluable due to its versatility. With the right dies, operators can bend metals to specific angles, a process that demands accuracy and repeatability. The authoritative control offered by hydraulic presses allows even the most complex metal fabrications to be undertaken with confidence.
Safety and accuracy are paramount in operations involving immense pressure. Therefore, operators are advised to follow stringent safety protocols. Proper setup of the workpieces, ensuring they are aligned and securely held, prevents accidental ejection under pressure. Wearing protective gear and conducting routine equipment checks also reinforces a safe working environment.
10 ton hydraulic shop press
The expertise surrounding the usage of a hydraulic shop press extends to its maintenance. Understanding both the mechanical and hydraulic systems enhances longevity and operational efficiency. Regular inspection and timely replacement of worn seals and other components ensure the equipment operates at peak performance, minimizing downtime.
Judging the quality of a 10-ton hydraulic shop press involves scrutiny of its build and specifications. Leading industry experts suggest scrutinizing the frame construction; a robust build not only ensures durability but also impacts safety during operations. Likewise, a reliable hydraulic system should have a smooth, responsive action, devoid of any erratic behavior.
Choosing the right shop press involves doing thorough market research. There are numerous manufacturers worldwide, but opting for reputable brands with certifications ensures you are investing in quality. Reviews and recommendations from trusted sources and industry veterans provide valuable insights that aid decision-making.
Transparency in operations promotes trustworthiness. By documenting press operations and maintenance activity systematically, operators can ensure compliance with safety standards and enhance accountability. It also makes troubleshooting easier, providing a clear history of use and care.
Ultimately, a 10-ton hydraulic shop press stands out as more than just a tool—it's a reliable partner in the workshop that significantly enhances productivity. Through expert use and diligent maintenance, it contributes to precise, efficient, and safe manufacturing processes, embodying not only capability but also the trust its users place in its consistent performance.