Navigating the world of industrial equipment reveals a plethora of tools designed to simplify complex tasks and optimize productivity. Among these,
the 50-ton air hydraulic shop press stands out as a formidable ally for professionals tackling heavy-duty tasks. This piece of machinery, often residing in automotive repair shops and metalworking industries, offers unparalleled capability in terms of strength and precision.
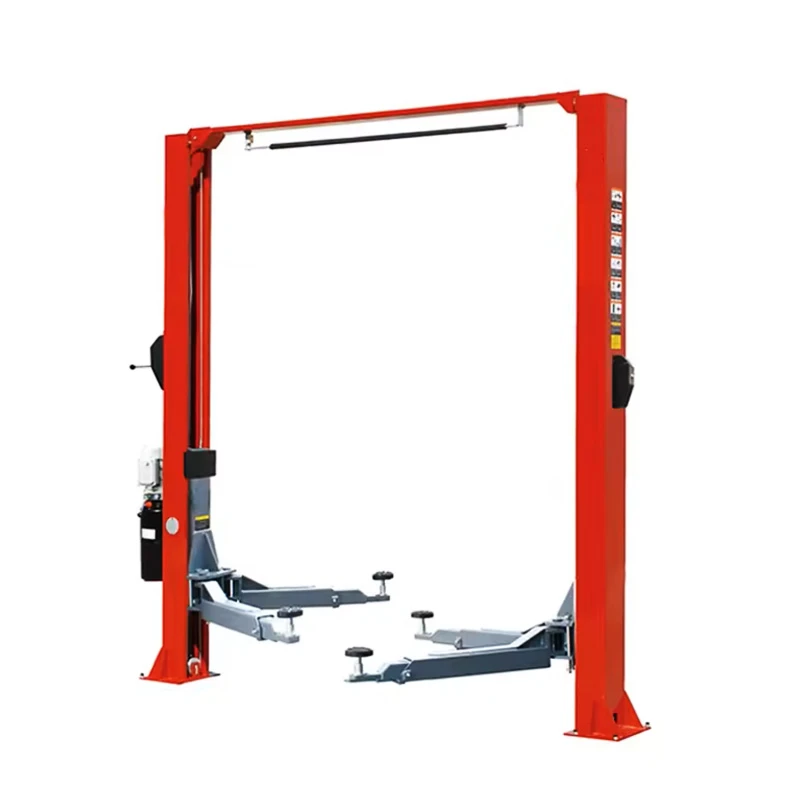
The core of what makes the 50-ton air hydraulic shop press indispensable is its dual-resource mechanism harnessing both air and hydraulic power. This hybrid operation allows for a seamless translation of minimal manual effort into substantial force, providing an efficient solution for bending, straightening, and pressing applications. This not only boosts productivity but also minimizes the risk of operator fatigue, contributing to a safer working environment.
Professionals who have extensively utilized the 50-ton air hydraulic shop press often highlight its reliability in delivering precise outcomes. This press’s durability is further exemplified by its rugged construction, which ensures stability even under full load operation. The quality of welds, the robust nature of the frame, and the precision of the pressing plates are aspects frequently mentioned in positive reviews, testifying to the product’s structural integrity and the manufacturer's commitment to excellence.
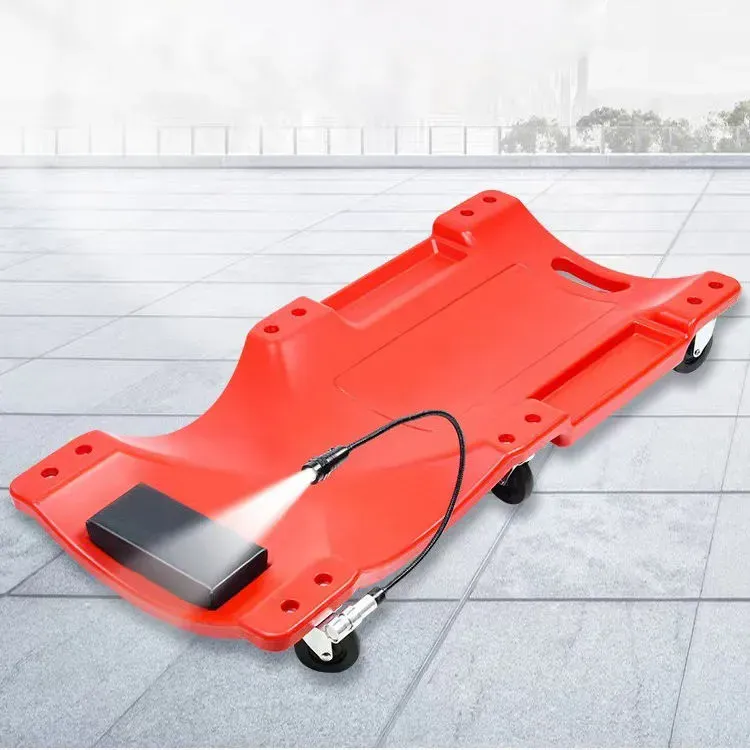
In terms of expertise, mastering the use of this machine unlocks numerous potentials across various sectors. The ability to apply sustained pressure effortlessly is crucial in complex repair jobs, such as removing and installing bearings, gears, and bushings. For fabricators, the precision and adaptability of the 50-ton press allow for more intricate and exact modifications, elevating the quality of the finished product.
Education on proper use, maintenance, and safety measures is crucial for operators who wish to maximize their use of the 50-ton air hydraulic shop press. Professional training ensures that users are not only familiar with the machine’s capabilities but also conversant with standard safety protocols—critical when operating machinery of this caliber. Efficient usage reduces wear and tear and prolongs the press’s lifespan, ensuring it remains a staple in the workshop.
50 ton air hydraulic shop press
From a perspective of authoritativeness, the 50-ton air hydraulic shop press is a staple tool recognized by industry veterans as essential equipment. Manufacturers of these shop presses often provide extensive warranties and multiple certifications, further reinforcing confidence in their reliability and operational longevity. These marks of quality are often a deal-breaker for businesses that require consistent performance without frequent downtimes.
Establishing trust in such equipment involves transparent communication regarding the press’s capabilities, limitations, and compatibility with various components. Comprehensive instruction manuals, readily available spare parts, and responsive customer service are vital in nurturing this trust. Businesses frequently make repeat purchases based on these factors, as they affirm the manufacturer’s commitment to customer satisfaction and support.
Furthermore, technological advancements have begun to influence the development of updated models of the 50-ton air hydraulic shop press. Features such as digital pressure gauges, improved pressure regulation systems, and environmentally friendly hydraulic fluids are enhancing the efficiency and eco-friendliness of newer models. These innovations not only appeal to eco-conscious businesses but also align with the evolving industry standards that emphasize sustainability and reduced carbon footprints.
In conclusion, the 50-ton air hydraulic shop press is more than a mere tool; it's an investment in precision, efficiency, and reliability. It’s an essential component for industries requiring heavy-duty pressing services. Beyond its immediate functionality, its value extends into the assurance it brings to professionals who demand nothing but the best in their workshops. Investing in such machinery is a step towards operational excellence, ensuring that work outcomes meet stringent industry demands while also paving the way for innovations in process and productivity efficiency.