Building a hydraulic shop press can be an exciting and rewarding project that combines technical skill with practical application. For machinists, mechanics, and DIY enthusiasts, a hydraulic shop press is an invaluable tool designed to exert significant force when bending, stamping, or pressing out components.
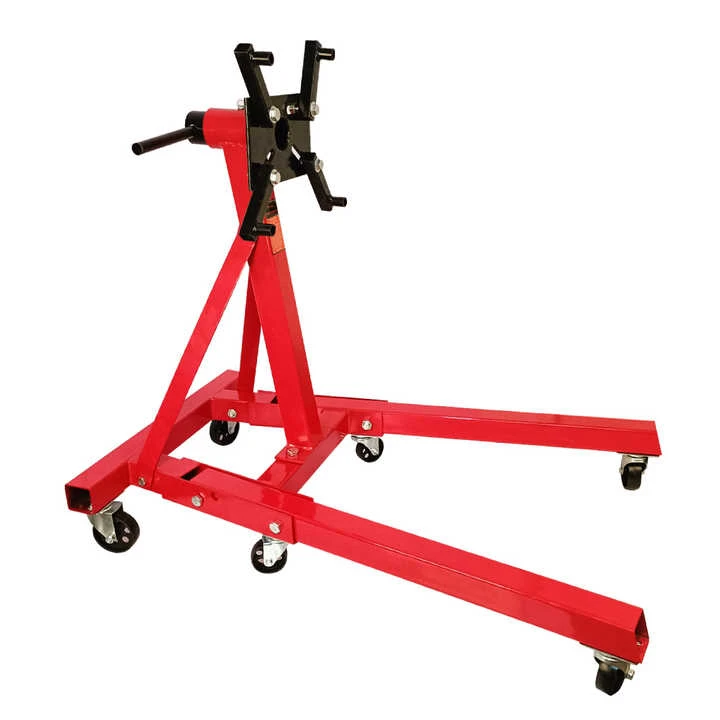
The essence of constructing a hydraulic shop press lies in understanding the mechanics of hydraulics, which harness the power of fluid pressure to produce forceful movement. A typical shop press includes a frame, a hydraulic jack, a pressing bed, and various accessories. Let us delve into the experience, expertise, authoritativeness, and trustworthiness required to create a reliable hydraulic press.
Before embarking on this construction, acquiring a fundamental understanding of hydraulic systems is mandatory. Hydraulic systems work on the principle of Pascal’s Law, which states that pressure applied to an enclosed fluid is transmitted equally in all directions. Comprehending this underlying principle ensures the project is rooted in sound engineering practices.
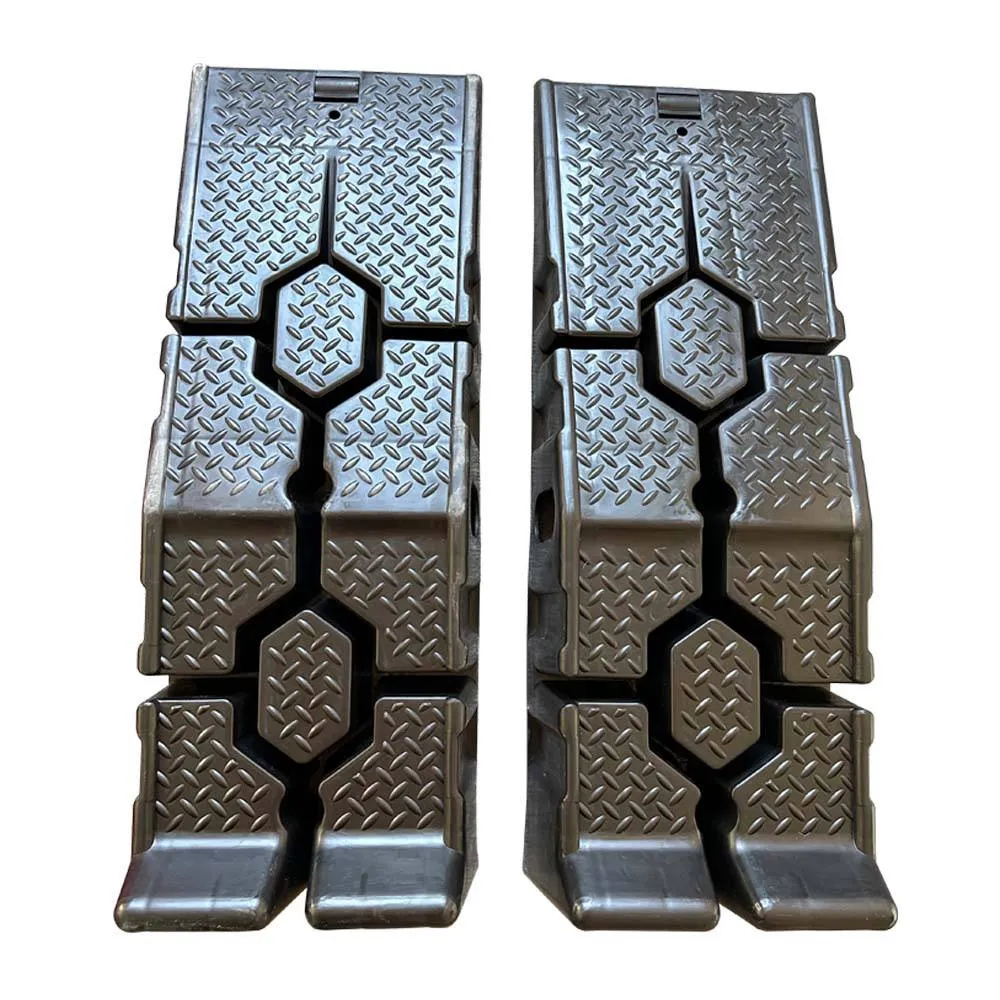
When selecting materials for your hydraulic shop press, focus on sourcing high-quality steel or iron for the frame. The frame is the backbone, providing support and stability during the press operation. For the hydraulic jack, ensure you choose one that meets your pressing capacity needs – commonly, a 20-ton or 30-ton jack suffices for most medium-level applications.
The construction phase demands meticulous attention to detail. Begin by cutting and welding the steel frame according to precise measurements. The corners should be reinforced to withstand the tremendous pressure exerted during operations. Installing safety guards can prevent accidents, thus enhancing trustworthiness and promoting a safe working environment.
Expert knowledge in welding and metal fabrication is crucial when assembling the press frame. Proper welding ensures the frame's integrity and longevity. For novices, consulting with experienced welders or taking courses in metal fabrication can elevate the construction quality.
building a hydraulic shop press
Assembling the hydraulic system requires precision. The hydraulic jack must be mounted securely onto the frame. If available, employing a pressure gauge provides insights into the system’s performance by indicating operational pressure levels. This addition also adds an extra layer of safety and assurance, affirming the system's reliability.
Once assembled, testing the press is a critical step. Start with low-pressure applications and gradually increase to assess the press’s full capability. Testing serves as a validation process, guaranteeing that the press operates optimally under various conditions. Failure to thoroughly test can lead to potential breakdowns, compromising both safety and trustworthiness.
To bolster your project's authoritativeness, documenting the entire process offers substantial value. Create a detailed guide, complete with diagrams and photographs, showcasing each construction step. Share this documentation online or within professional circles to establish credibility and contribute to the community of hydraulic machinery enthusiasts.
Trustworthiness in constructing a hydraulic shop press is further solidified through observing all safety standards and best practices. Regular maintenance checks, such as inspecting for leaks or worn-out parts, ensure long-term performance and enhance the press's trust factor.
In conclusion, building a hydraulic shop press is an enriching project that bridges experience, expertise, and safety into a practical outcome. By adhering to robust engineering principles, leveraging expert guidance, and ensuring thorough testing and documentation, one can construct a reliable shop press that stands as a testament to skill and precision. This not only elevates personal craftsmanship but also enriches the community, contributing to a wealth of shared knowledge and innovation.