Workshop press tools serve as integral components in various industrial settings, offering unparalleled efficiency and precision. These tools are not merely machines; they represent a blend of engineering innovation and practical utility, designed to support and enhance a multitude of fabrication processes. Understanding their capabilities and applications can significantly benefit users in terms of productivity and quality of output.
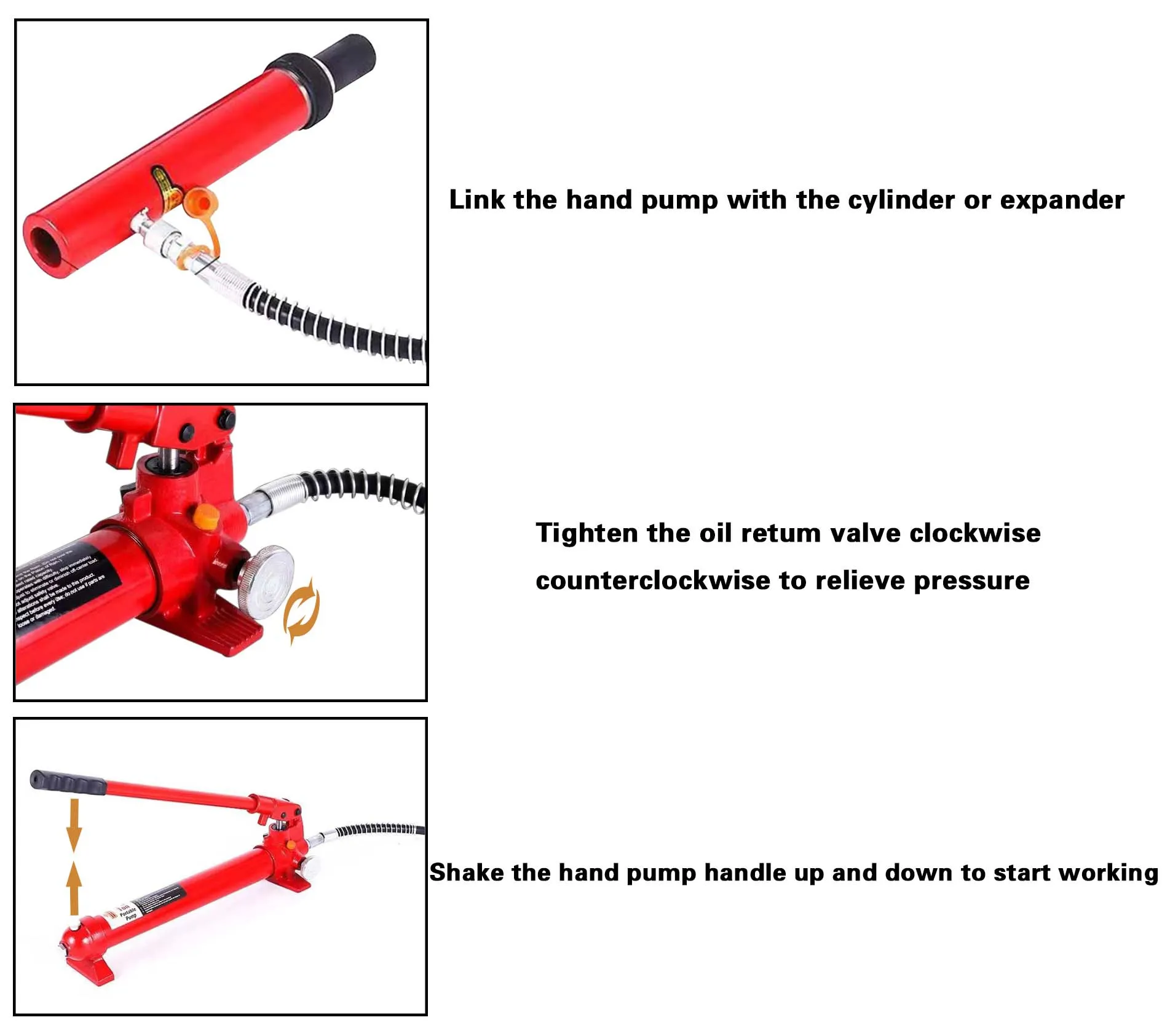
Workshop press tools are primarily used for shaping, cutting, and assembling materials, predominantly metals. Their primary function is to apply pressure to different workpieces, which transforms raw materials into finished products. Users have a range of options when it comes to these presses, from hydraulic to mechanical systems, each offering distinct advantages based on specific needs.
Hydraulic press tools are particularly renowned for their versatility and precision. They operate through hydraulic cylinders that provide consistent pressure, making them ideal for tasks requiring detailed and repetitive actions. Industries leveraging these presses include automotive manufacturing, where precise forming of metal sheets into car parts is crucial. The ability to control pressure precisely allows for the creation of complex shapes that are consistent in quality, an essential factor in mass production.
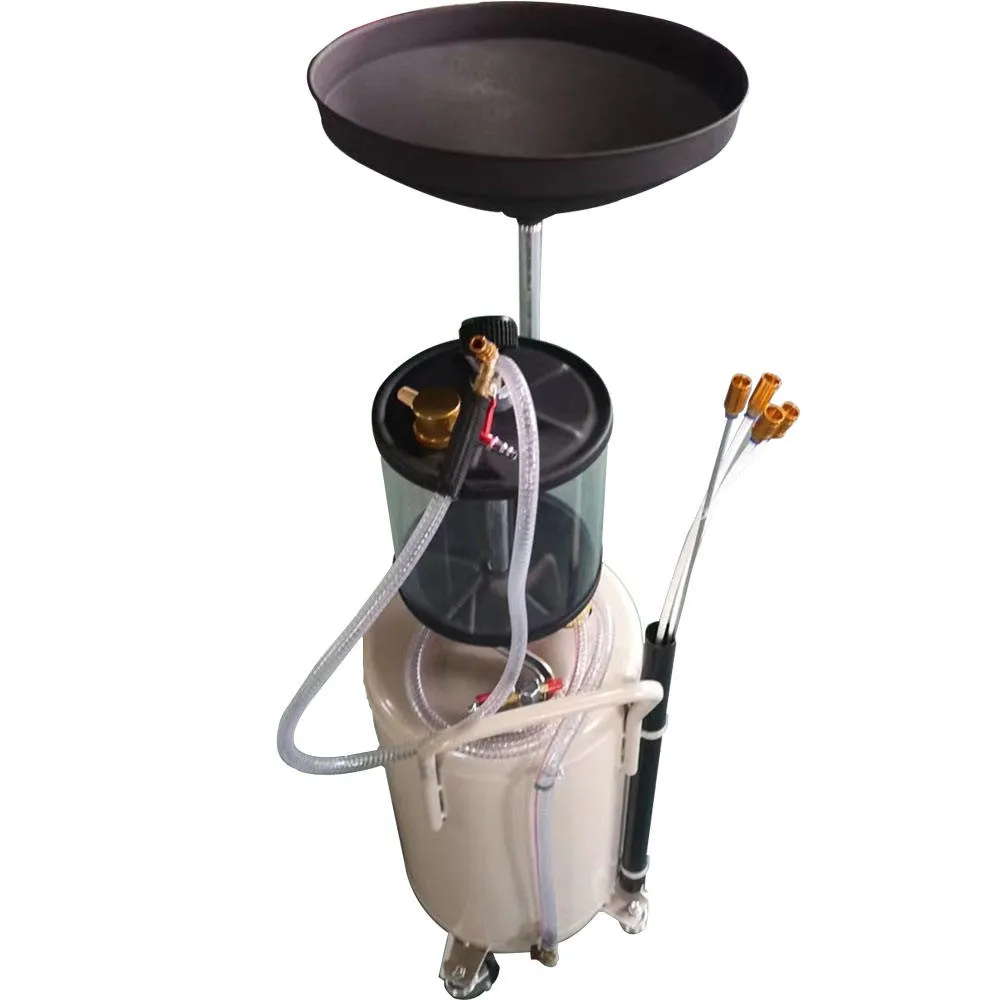
Mechanical presses, on the other hand, boast speed and efficiency. They are typically employed in operations where high output is necessary, such as stamping and shearing. Although they may not offer the same level of precision as hydraulic presses, their speed of operation makes them indispensable in high-volume production lines. Material handling becomes simpler with mechanical presses due to their rapid cycle times, which reduce turnaround times and increase overall throughput.
workshop press tools
For workshops considering an investment in press tools, it is critical to assess the specific requirements of their operations. Factors such as the type of material being processed, the desired speed of operation, and the precision needed in the final product should dictate the choice between hydraulic and mechanical systems. Additionally, workshop space and power supply capabilities must be evaluated to ensure the compatibility and efficient operation of the chosen press tool.
Maintenance of workshop press tools is another essential consideration. Well-maintained machines not only last longer but also perform more reliably, thereby guaranteeing the quality of the processed materials. Regular inspections and timely servicing help in identifying wear and tear early, reducing the chances of unexpected breakdowns. Having a preventive maintenance schedule can minimize downtime and extend the lifetime of the equipment, yielding a better return on investment.
Safety is paramount when operating workshop press tools. It is crucial to adhere to safety guidelines and provide adequate training for all operatives. Proper use of safety gear, such as gloves and goggles, and ensuring the presence of emergency stop mechanisms can mitigate the risk of workplace accidents. Furthermore, automated systems integrated with modern press tools can enhance safety by reducing the need for direct human intervention.
In conclusion, workshop press tools are vital assets in any industrial setting where materials need to be shaped and assembled accurately and efficiently. Choosing the right type of press, understanding its operational nuances, maintaining the equipment, and prioritizing safety can optimize performance and productivity. By leveraging the unique strengths of hydraulic and mechanical presses, workshops can significantly enhance their fabrication processes, achieving high-quality results with increased operational efficiency.