The concept of a workshop press is transforming the industrial landscape by offering unparalleled advantages in manufacturing and repair contexts. Workshop presses, also known as hydraulic presses, are essential pieces of machinery used to bend, straighten, or press materials with precision and control, thereby enhancing operational efficiency.
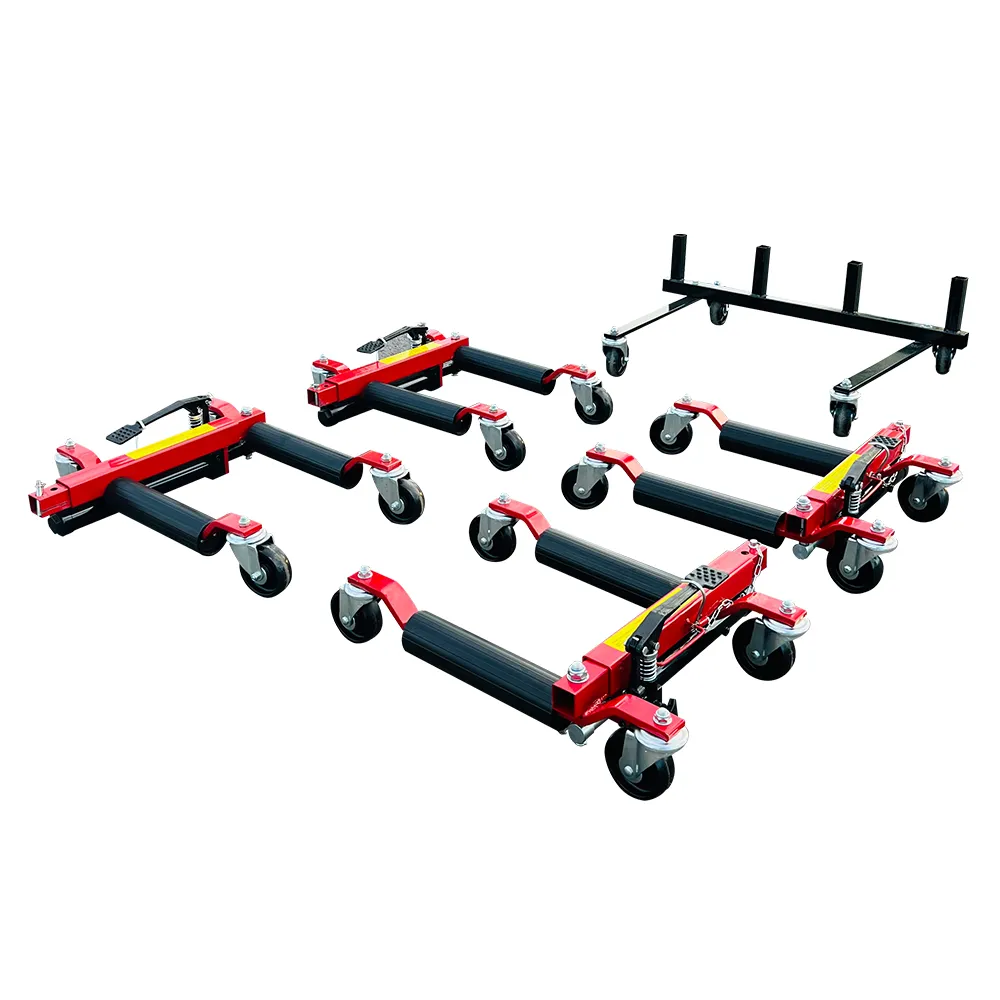
Experience plays a crucial role in the optimal use of a workshop press. Individuals interacting with these devices must comprehend the subtleties of material deformation and the appropriate application of force. A skilled operator understands the machine's nuances, from adjusting the pressure settings to accommodating various material types. This intimate knowledge not only ensures the safety of operations but also maintains the integrity of the workpieces involved, preventing damage or waste.
From an expertise standpoint, workshop presses are fundamental tools that demand a sophisticated understanding of hydraulics and mechanics. These machines typically leverage hydraulic force, an advantage because it provides consistent and controllable pressure. Professionals equipped with expertise in fluid dynamics and engineering are indispensable, as they can diagnose and rectify inefficiencies or faults in the system. In-depth knowledge of the press components—such as the hydraulic pump, ram, and bed—enables technicians to make informed decisions concerning maintenance and upgrades, thereby extending the lifespan of the equipment.
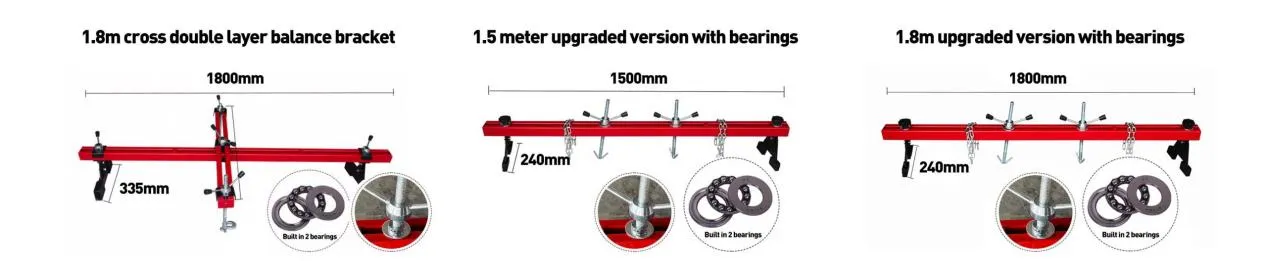
The authoritativeness regarding workshop presses is underscored by their universal application across diverse industries. Whether in automotive repair shops, metal fabrication facilities, or assembly lines, workshop presses are trusted for their reliability and versatility. Their authoritative presence is backed by a historical track record of revolutionizing processes that require precision forming or material assembly. Leading manufacturers consistently update these machines with advanced features like digital pressure readouts, programmable logic controllers, and energy-efficient systems, further validating their essential role in industrial operations.
workshop press
Trustworthiness in the context of a workshop press is critical, as operators rely on this equipment for repeatable and consistent results. Trust is built through rigorous quality assurance processes during manufacturing and stringent adherence to safety standards.
Workshop presses are usually subjected to exhaustive testing and certification to ensure they meet international safety guidelines. This level of scrutiny provides users with confidence in the machine's reliability, minimizing downtime due to unforeseen mechanical failures.
In the realm of product optimization, workshop presses can significantly impact the quality and efficiency of industrial output. When integrated into production lines, their ability to consistently produce uniform parts reduces material wastage and ensures alignment with design specifications. This efficiency translates into cost savings and increased production capacity, enabling companies to fulfill orders on time and with high precision.
As industries continue to evolve, so does the technology behind workshop presses. Innovations such as smart sensors that monitor pressure and temperature in real-time are becoming standard, allowing for predictive maintenance and reduced operational interruptions. These advancements position workshop presses as indispensable tools for future-forward manufacturing processes, ensuring they remain relevant in an ever-changing industrial landscape.
In conclusion, the workshop press is more than just a mechanical apparatus; it embodies the core principles of Experience, Expertise, Authoritativeness, and Trustworthiness. Mastery of these machines not only secures operational success but also adapts seamlessly to the demands of modern industry, making them an invaluable asset to any production environment.