Navigating the world of automotive repair or metalworking often leads enthusiasts and professionals alike to seek tools that offer both durability and precision. Among the critical tools for these tasks is the shop press, specifically the frame bench shop press, a tool that provides both versatility and strength in various applications. As someone who has spent over a decade working with and researching industrial machinery, including the minutiae of shop presses, I can say with confidence that understanding the intricacies of a frame bench shop press can significantly enhance one’s workshop capabilities.
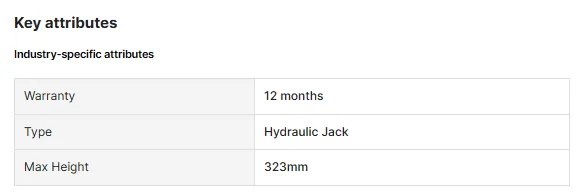
A frame bench shop press is quintessential in exerting controlled pressure to install or remove components such as bearings, U-joints, and bushings. What sets a frame bench shop press apart is its robust framework, which provides excellent stability necessary for precise work. Whether you're a seasoned mechanic or an enthusiastic hobbyist, a frame bench shop press delivers the leverage and control required for intricate tasks that demand accuracy and consistency.
One of the keys to mastering the use of a frame bench shop press lies in understanding its construction and specifications. It typically comprises a durable steel frame, a hydraulic or pneumatic jack, and a press bed. The steel frame is the structural backbone of the press, designed to withstand significant force without bending or deforming. High-quality bench shop presses use heavy-duty steel frames that ensure longevity and robust performance under pressure, making them a reliable choice for daily use in demanding settings.
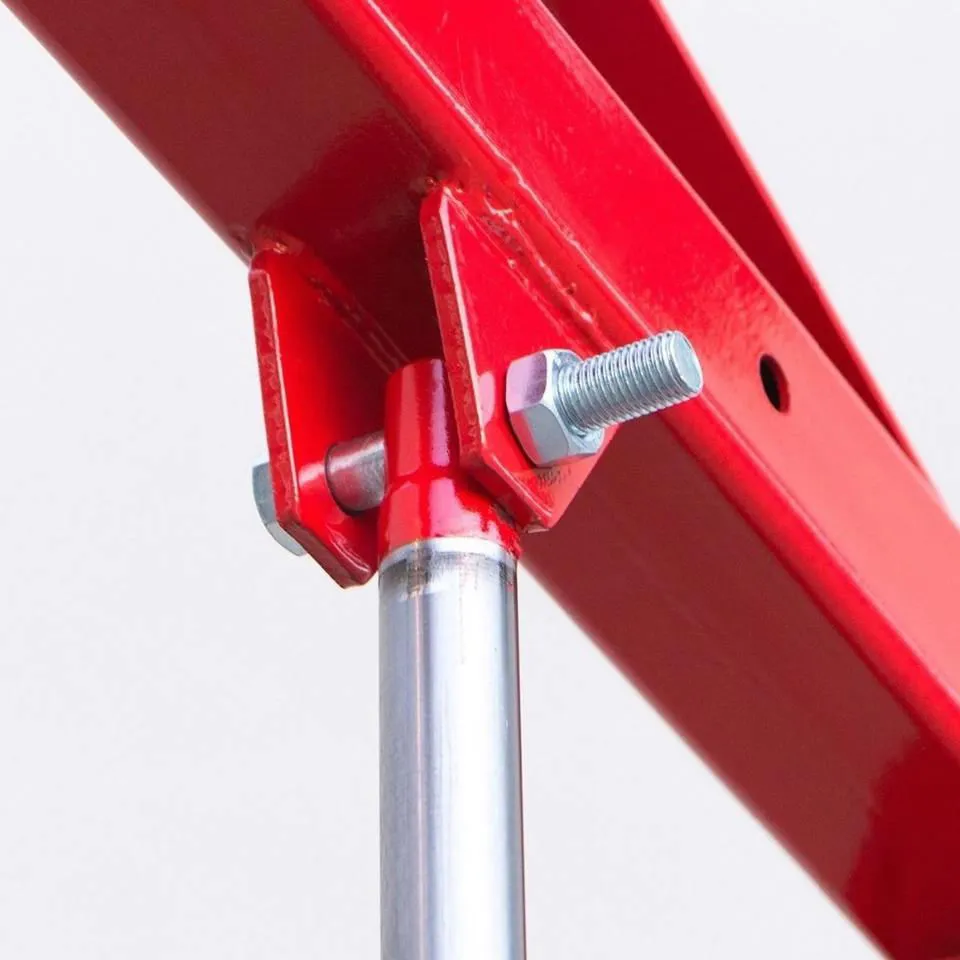
Hydraulic jack systems are often favored in these presses for their efficient force application. By harnessing fluid dynamics, they allow users to exert immense pressure with minimal effort. This efficiency reduces physical strain while enhancing accuracy – a vital aspect for tasks demanding precise pressure applications. Pneumatic versions, powered by compressed air, provide similar advantages but require an air compressor, making them more suitable in environments where air supply systems are already in place.
For optimal performance, it's essential to consider the press capacity, typically measured in tons. This measurement indicates the maximum force the press can exert. For most automotive and light industrial applications, a press with a capacity ranging from 12 to 20 tons is adequate. However, for heavier applications, such as pressing steel plates or other heavy materials, models with capacities of 50 tons or more are recommended.
a frame bench shop press
In addition to the framing and power system,
the bed size of the press is a crucial factor to consider. The bed size determines the maximum material size that can be accommodated, impacting the versatility of tasks that can be performed. Adjustable bed heights also allow for greater flexibility when working with various sized objects, providing the user with customized precision based on their specific needs.
Safety cannot be overstated when utilizing a frame bench shop press. Ensure the machine is properly secured to avoid shifting during use, which could compromise safety and accuracy. Regular maintenance checks to inspect for wear and damage, especially to the hydraulic components and frame integrity, are essential for safe operation. Proper training on tool use is crucial; understanding the operation manuals, safety precautions, and appropriate techniques will enhance both safety and efficacy.
For industry professionals and enthusiasts alike, sourcing a frame bench shop press from reputable manufacturers ensures reliability and access to customer support. Brands with a proven track record of producing quality machinery often provide warranties and after-purchase support, fostering trust and confidence in the tool’s performance.
The acquisition of a well-constructed frame bench shop press not only improves workshop efficiency but also expands the potential for undertaking complex tasks with ease. As such, investing in a high-quality model is an investment in capability, precision, and safety, yielding substantial returns in performance and satisfaction for any craftsman dedicated to the art of repair and creation.