Building a shop press can be a rewarding endeavor that bolsters your workshop's efficiency and broadens the range of projects you can undertake. When constructing a shop press, several critical considerations must be met to ensure the press not only functions as expected but also maintains safety and durability standards. This guide provides an in-depth exploration of crafting a shop press, drawing on industry expertise and real-world experience to ensure your project is a success.
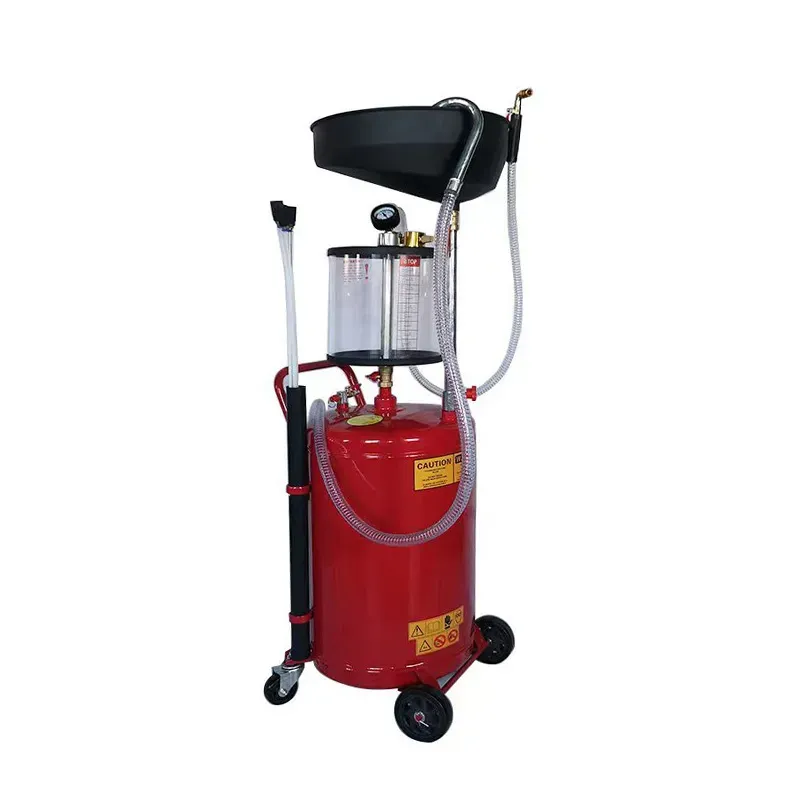
Choosing the Right Materials
The selection of appropriate materials is the cornerstone of creating a reliable shop press. Start with a sturdy steel frame, as the backbone of your press must withstand substantial force. Mild steel, renowned for its strength and workability, is often sufficient for DIY projects, but if you anticipate heavy-duty usage, opt for something more robust like structural steel.
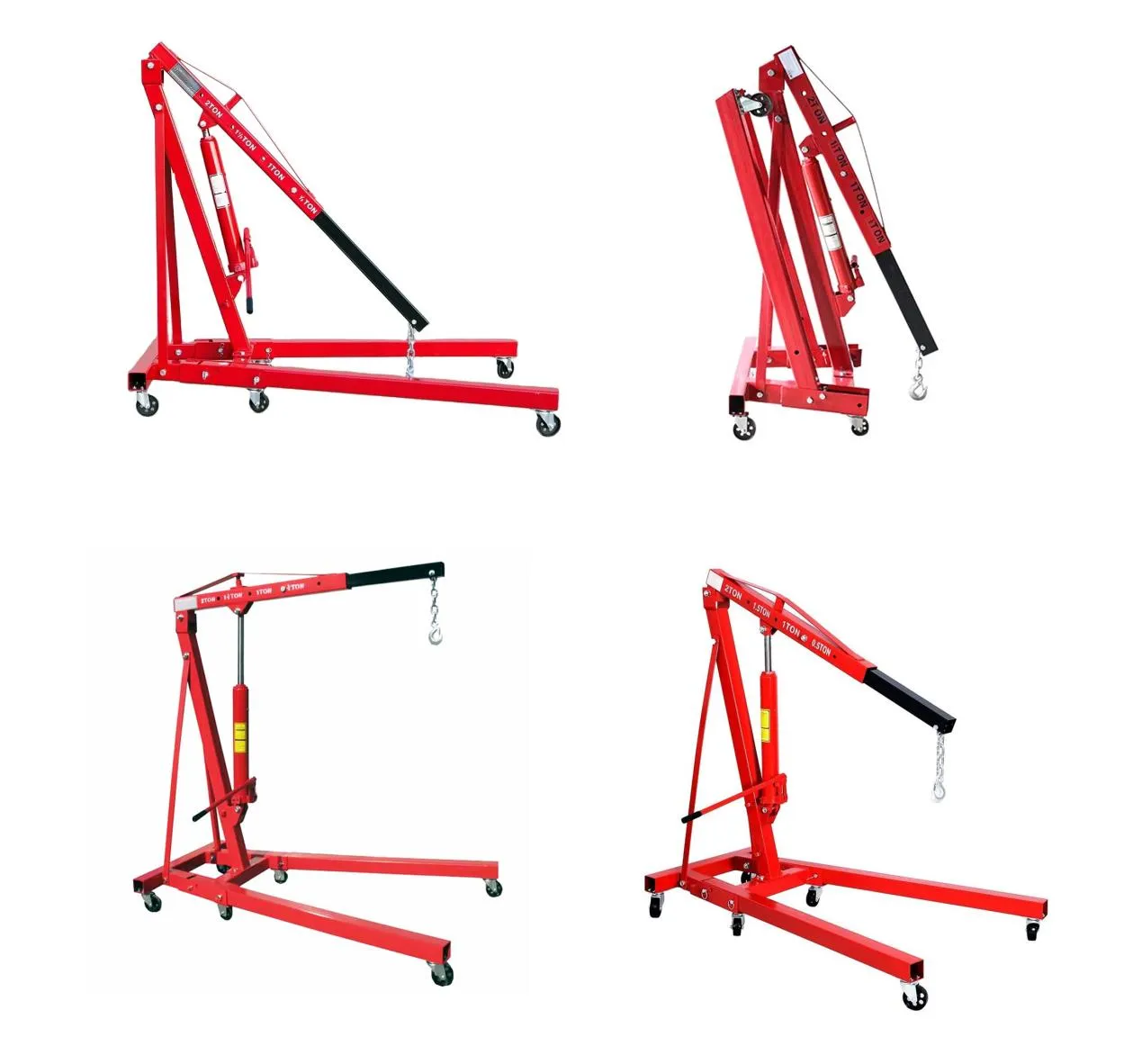
Hydraulic System Essentials
At the heart of any shop press is the hydraulic system, which applies the necessary force. Investing in a high-quality hydraulic bottle jack is crucial. Jacks are available in various tonnage ratings; choosing one with a higher capacity than the maximum force you'll need provides a safety margin and avoids overloading. Ensure the hydraulic system is compatible with your intended uses, whether pressing bearings or bending metal sheets.
Design Considerations
A well-thought-out design enhances both functionality and safety. Your shop press should feature a wide base for stability and an adjustable bed height to accommodate different workpiece sizes. Draw on engineering principles to calculate force distribution across the press structure, minimizing stress on any single component which reduces the risk of structural failure. Incorporate guidance from finite element analysis if possible, or consult with a professional to validate your design under load conditions.
making a shop press
Assembly and Fabrication Techniques
Precision in joining materials is essential in ensuring a robust assembly. Welding is the preferred method for joining steel components, offering strength and rigidity. Ensure welds are clean and penetrate well into the materials, and perform non-destructive testing to verify weld integrity if possible. Pre-drill holes and tap threads accurately, which ensures bolts and other fasteners seat snugly, contributing to overall structural integrity.
Safety Features and Testing
Safety should never be an afterthought.
Incorporate safety stops and guards to prevent accidents. A pressure relief valve within the hydraulic system is a crucial safety component, preventing overloads that could cause catastrophic failure. Once assembled, conduct rigorous testing. Start with lower pressures and incrementally increase, observing for any signs of stress or failure in the structure. Regular inspections post-construction will help maintain operational safety and longevity.
Customizing for Enhanced Functionality
Customization can further extend the utility of your shop press. Consider adding a set of V-blocks to support cylindrical workpieces or various dies for specific tasks like bending or stamping. Adjustable width and height features can greatly enhance versatility, allowing you to modify the press setup based on the unique needs of each project.
By adhering to these principles and leveraging expert insights, you create a shop press that's not only functional but tailored to your workshop's specific demands. Investing time and effort in selecting quality materials, designing with precision, and assembling with care combines to create a tool that's safe, reliable, and capable of meeting your projects' demands. This holistic approach not only enhances the performance of your press but also ensures it stands as a testament to skilled craftsmanship—a key asset in any high-functioning workshop.